connecting wires together
#1
Advanced


Thread Starter
Member Since: Jun 2015
Location: huntingdale western australia
Posts: 85
Received 2 Likes
on
2 Posts

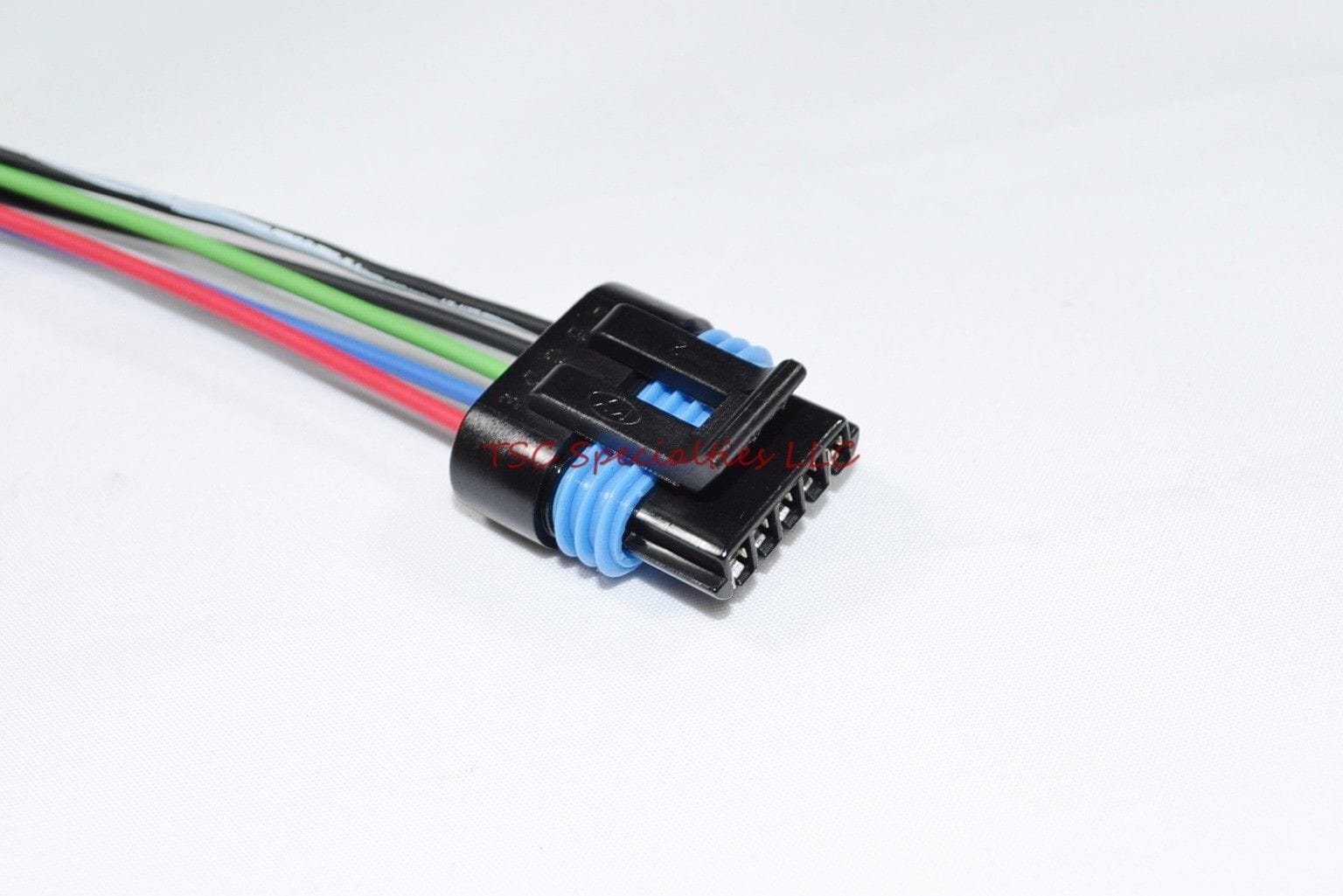
MAF sensor connector and pigtails
hi guys just ordered this and just wondering what the best way is to connect the wires together in the engine bay , Cheers and thanks in advance

The following users liked this post:
bullguts (08-07-2016)
#3

typically, I use a type, or variation, of the linesman splice - solder, and shrink sleeving. try google - plenty of examples -

Last edited by Joe C; 08-07-2016 at 12:33 AM.
The following users liked this post:
bullguts (08-07-2016)
#4
Advanced


Thread Starter
Member Since: Jun 2015
Location: huntingdale western australia
Posts: 85
Received 2 Likes
on
2 Posts

ok , thanks for that and was actually thinking along those lines but, there seems to be a wide range of connectors out there . Some actually say that , solder is not a good conductor and heating the wire makes it brittle . Cheers

#5



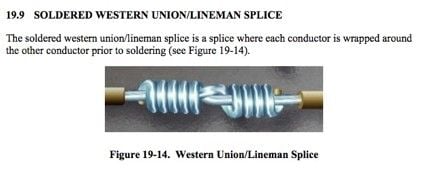
Last edited by Joe C; 08-07-2016 at 02:34 AM.
The following 2 users liked this post by Joe C:
bullguts (08-07-2016),
ChrisWhewell (08-09-2016)
#6
Melting Slicks



Solder is not your friend with anything subject to vibration. Brased seam uninsulated butt splices a proper W form crimper and heat shrink with glue inside it.
The following users liked this post:
bullguts (08-07-2016)
#7

I believe that a GOOGLE search for "Environmental Splice" will get you appropriate information. A five wire also has it's challenges - stagger the splices in a reasonable range. Add "aircraft" to the search term maybe.
The correct crimping device is important
Had you not already ordered I'd suggested maybe a connector shell and terminals BUT the one you imaged has it's own challenges. It's "pull to seat" and you can't release and insert, you need to pass the wire through first, add terminals and then pull back into the shell. I wouldn't have a problem with it because I've done them. Correct crimping device required again.
Last edited by WVZR-1; 08-07-2016 at 08:24 AM.
The following users liked this post:
bullguts (08-07-2016)
#8
Melting Slicks



In these times I'd go with this technique vs most any other. In the 80's/90's I'd likely have used the Delphi splice clips shown in the FSM for the C4's. I've used many/many of them.
I believe that a GOOGLE search for "Environmental Splice" will get you appropriate information. A five wire also has it's challenges - stagger the splices in a reasonable range. Add "aircraft" to the search term maybe.
The correct crimping device is important
Had you not already ordered I'd suggested maybe a connector shell and terminals BUT the one you imaged has it's own challenges. It's "pull to seat" and you can't release and insert, you need to pass the wire through first, add terminals and then pull back into the shell. I wouldn't have a problem with it because I've done them. Correct crimping device required again.
I believe that a GOOGLE search for "Environmental Splice" will get you appropriate information. A five wire also has it's challenges - stagger the splices in a reasonable range. Add "aircraft" to the search term maybe.
The correct crimping device is important
Had you not already ordered I'd suggested maybe a connector shell and terminals BUT the one you imaged has it's own challenges. It's "pull to seat" and you can't release and insert, you need to pass the wire through first, add terminals and then pull back into the shell. I wouldn't have a problem with it because I've done them. Correct crimping device required again.

Last edited by s carter; 08-07-2016 at 11:07 AM.
The following users liked this post:
bullguts (08-07-2016)
#9

I strip the ends of each a pretty good length, slip a shrink sleeve over one side, then twist braid the two wire ends together so they're linear, touch it with a solder iron and let the solder flow through the wrap. Then, one wrap of electrical tape and then slide the heat shrink sleeve over it and hit it with the effluent of a propane torch, not the flame part, just the hot air. Probably a crimp sleeve is quicker, but my connections never fail until after I'm in the ground

The following users liked this post:
bullguts (08-07-2016)
#10

In these times I'd go with this technique vs most any other. In the 80's/90's I'd likely have used the Delphi splice clips shown in the FSM for the C4's. I've used many/many of them.
I believe that a GOOGLE search for "Environmental Splice" will get you appropriate information. A five wire also has it's challenges - stagger the splices in a reasonable range. Add "aircraft" to the search term maybe.
The correct crimping device is important
Had you not already ordered I'd suggested maybe a connector shell and terminals BUT the one you imaged has it's own challenges. It's "pull to seat" and you can't release and insert, you need to pass the wire through first, add terminals and then pull back into the shell. I wouldn't have a problem with it because I've done them. Correct crimping device required again.
I believe that a GOOGLE search for "Environmental Splice" will get you appropriate information. A five wire also has it's challenges - stagger the splices in a reasonable range. Add "aircraft" to the search term maybe.
The correct crimping device is important
Had you not already ordered I'd suggested maybe a connector shell and terminals BUT the one you imaged has it's own challenges. It's "pull to seat" and you can't release and insert, you need to pass the wire through first, add terminals and then pull back into the shell. I wouldn't have a problem with it because I've done them. Correct crimping device required again.




http://www.aircraftspruce.com/catalo...ptoolgm232.php
no flames, and not to be a wise ***, but seriously, (and to the OP) don't over think this, and use the KISS. approach - strip the wire, lineman twist, solder, and shrink sleeving. as far as "solder is not your friend with anything subject to vibration," not sure where anyone's going with that. secure the harness repair on both side of the splice(s) with a couple tie-wraps. this isn't a mission to mars -

BTW, just my 2-cents....
Last edited by Joe C; 08-07-2016 at 08:55 PM.
The following users liked this post:
bullguts (08-07-2016)
#11
Race Director



Here's a different spin. Can you re-pin the new connector? No splicing needed.
I work at a GM facility. Soldering is not a GM approved repair technique. We only use heat shrink butt splices.
I work at a GM facility. Soldering is not a GM approved repair technique. We only use heat shrink butt splices.
The following users liked this post:
bullguts (08-08-2016)
#12
Advanced


Thread Starter
Member Since: Jun 2015
Location: huntingdale western australia
Posts: 85
Received 2 Likes
on
2 Posts


#13

to be honest this the second time around for me , first time around bought the connector shell and pins and crimp the wires onto them , type of deal . I obviously failed dismally doing it that way because it all came apart when I pulled the sensor off . Tried soldering the pins to the wires and ended up breaking one of the pins . Lesson learned , and thanks to every one for your help , cheers .

I doubt "JoeC's" comment of a "couple hundred bucks" is required for the "Environmental Splice" BUT if you own an older C4 sooner or later quality cut/splice and electrical connector assembly is going to be required. Quality tools makes most much easier.
Do you have issues with getting parts in your location?
The following users liked this post:
bullguts (08-08-2016)
#14
Advanced


Thread Starter
Member Since: Jun 2015
Location: huntingdale western australia
Posts: 85
Received 2 Likes
on
2 Posts

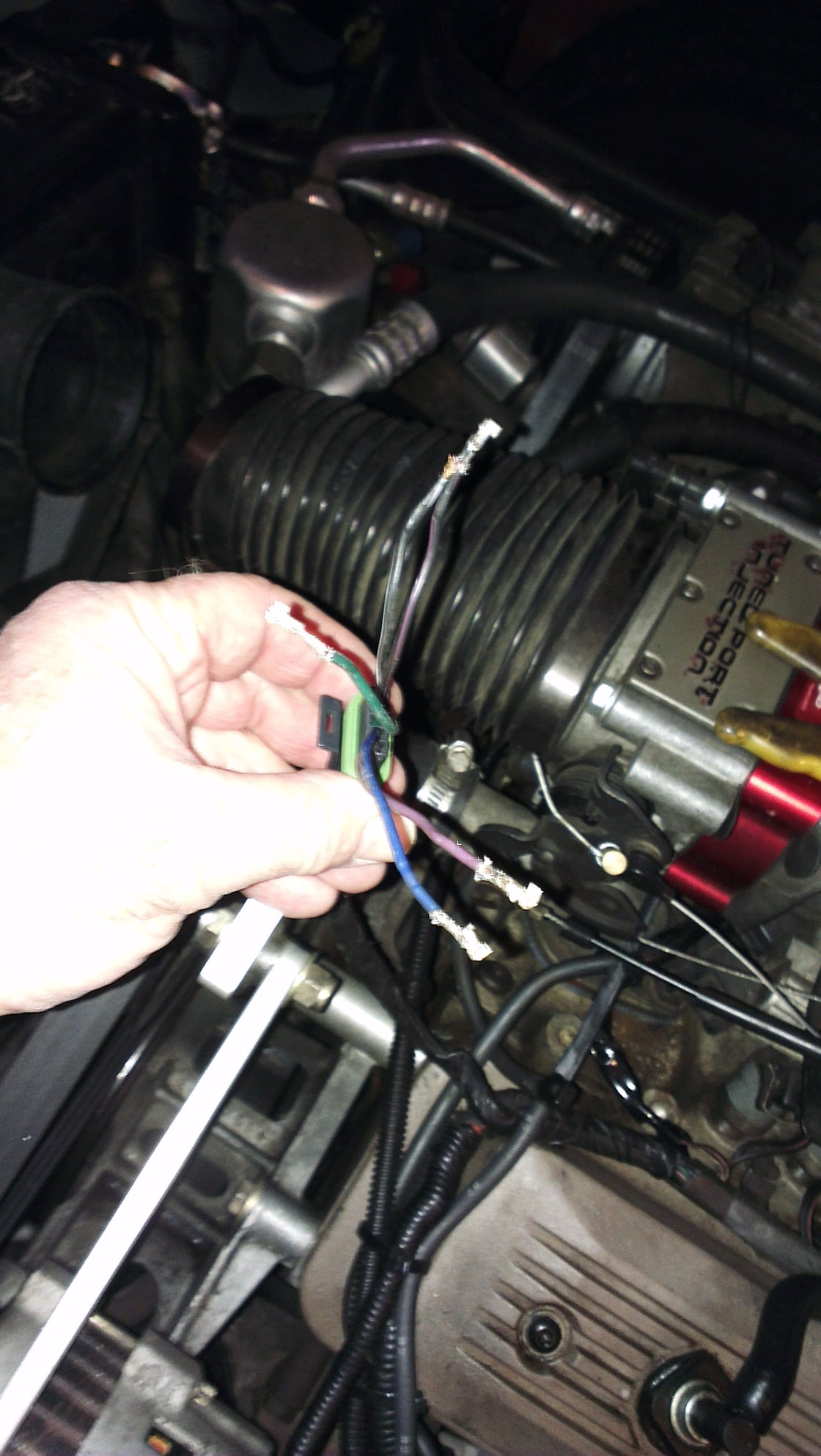
i looked a little closer at the connector image and it's likely a Delphi 150.2 and NOT a "pull to seat" like I mentioned earlier so I'd likely suggest the shell, terminals and seals all over again but maybe borrow/buy the crimping device or maybe just hire the assembly. Since you hinted the pig-tail is already ordered just do the cut splice whichever way you think best.
I doubt "JoeC's" comment of a "couple hundred bucks" is required for the "Environmental Splice" BUT if you own an older C4 sooner or later quality cut/splice and electrical connector assembly is going to be required. Quality tools makes most much easier.
Do you have issues with getting parts in your location?
I doubt "JoeC's" comment of a "couple hundred bucks" is required for the "Environmental Splice" BUT if you own an older C4 sooner or later quality cut/splice and electrical connector assembly is going to be required. Quality tools makes most much easier.
Do you have issues with getting parts in your location?

#15
Melting Slicks



i looked a little closer at the connector image and it's likely a Delphi 150.2 and NOT a "pull to seat" like I mentioned earlier so I'd likely suggest the shell, terminals and seals all over again but maybe borrow/buy the crimping device or maybe just hire the assembly. Since you hinted the pig-tail is already ordered just do the cut splice whichever way you think best.
I doubt "JoeC's" comment of a "couple hundred bucks" is required for the "Environmental Splice" BUT if you own an older C4 sooner or later quality cut/splice and electrical connector assembly is going to be required. Quality tools makes most much easier.
Do you have issues with getting parts in your location?
I doubt "JoeC's" comment of a "couple hundred bucks" is required for the "Environmental Splice" BUT if you own an older C4 sooner or later quality cut/splice and electrical connector assembly is going to be required. Quality tools makes most much easier.
Do you have issues with getting parts in your location?

I work in heavy industrial construction and have for 25 years. In all that time, I have only seen a soldering gun being used once or twice, and that was for very specialized applications where crimping was not practical.(applies to PC boards etc.). As I speak, we are completing a cement processing facility involving hundreds of instrumentation, power and PLC terminations. Not one piece of solder. Soldering is old school and rarely used today. However, there are people on this board that will never be convinced of this fact.
The following users liked this post:
bullguts (08-08-2016)
#16

Solder can't be all that bad, they use solder on the circuitboards in the ECM, ICM, Radio, climate control, etc. Crimps are faster, and profitability depends on labor costs, that's why crimps are used, they're "good enough" for now. Imagine building a radio and crimp connecting every component in the circuit, instead of using solder, lol

Last edited by ChrisWhewell; 08-08-2016 at 08:39 AM.
The following users liked this post:
bullguts (08-08-2016)
#17


I work in heavy industrial construction and have for 25 years. In all that time, I have only seen a soldering gun being used once or twice, and that was for very specialized applications where crimping was not practical.(applies to PC boards etc.). As I speak, we are completing a cement processing facility involving hundreds of instrumentation, power and PLC terminations. Not one piece of solder. Soldering is old school and rarely used today. However, there are people on this board that will never be convinced of this fact.

I think ChrisWhewell nailed it in his post - "crimps are faster, and profitability depends on labor costs." besides, less gray matter involved -

OP - keep it simple - crimp, solder, or whatever. fix the thing and move on. this ain't rocket science (or a dump truck)!

Last edited by Joe C; 08-08-2016 at 11:11 AM.
The following users liked this post:
bullguts (08-08-2016)
#18
Melting Slicks



old school, yes - well maybe, but "tried and true" still applies. there are still a bunch of people doing "old school" - just google "approved solder splicing wire." while there may be better, more current methods for repair, we're talking about a 5 wire, electrical connector repair on a 25 year old car, not some heavy industrial equipment or a processing facility with a bunch of high tech stuff. no flames, but some people tend to make things way more complicated than it needs to be, while others try to impress us with their technical expertise - 
I think ChrisWhewell nailed it in his post - "crimps are faster, and profitability depends on labor costs." besides, less gray matter involved -
OP - keep it simple - crimp, solder, or whatever. fix the thing and move on. this ain't rocket science (or a dump truck)!

I think ChrisWhewell nailed it in his post - "crimps are faster, and profitability depends on labor costs." besides, less gray matter involved -

OP - keep it simple - crimp, solder, or whatever. fix the thing and move on. this ain't rocket science (or a dump truck)!

The following users liked this post:
bullguts (08-08-2016)
#19

Sorry Joe C, I have no need to impress anyone with technical expertise - it is simply fact. Don't take my word for it, check any numerous websites. Google is there for everyone. Several industries ban solder because under certain short circuit conditions, a solder splice can melt whereas a crimp will not.
http://www.hq.nasa.gov/office/codeq/...NSTD87394A.pdf
but then again, our space program is kind of backwards.

if anyone experiences a "short circuit" condition that would cause solder to melt, the melting solder would be the least of their problems. I'm sure you know all about current limiting and circuit safety devices.

Last edited by Joe C; 08-08-2016 at 02:29 PM.
The following users liked this post:
bullguts (08-08-2016)
#20
Melting Slicks



...and what industries would that be? not to doubt your "technical expertise," but reference NASA-STD-8739.4A – 2016-06-30, page 70, section or paragraph 19.7 -
http://www.hq.nasa.gov/office/codeq/...NSTD87394A.pdf
but then again, our space program is kind of backwards.
.
if anyone experiences a "short circuit" condition that would cause solder to melt, the melting solder would be the least of their problems. I'm sure you know all about current limiting and circuit safety devices.
http://www.hq.nasa.gov/office/codeq/...NSTD87394A.pdf
but then again, our space program is kind of backwards.

if anyone experiences a "short circuit" condition that would cause solder to melt, the melting solder would be the least of their problems. I'm sure you know all about current limiting and circuit safety devices.


The following users liked this post:
bullguts (08-08-2016)