Center Outlet Exhaust
#82
Drifting



Bob, that looks great, I wasn't sure I would like the Camaro spoiler on the car, but you seemed to work you magic again to a job well done.
Thanks for sharing.
Riggs
Thanks for sharing.
Riggs
#83
Pro


Thread Starter

Amazing how a month just disappears....
Once I had the side sections of the spoiler pop riveted in place, I did the final fitting of the legs on the sides. Not sure it was the best way to improve the fit but it seems to have worked. I put a small wedge under the leg and slid a piece of 80-grit sandpaper into the gap. This is PSA (pressure sensitive adhesive) backed paper so it has a slippery backing sheet. It took a while but when I was done the wedge was no longer needed and the paper moved reasonably well (it still dragged but I could move it with no trouble).
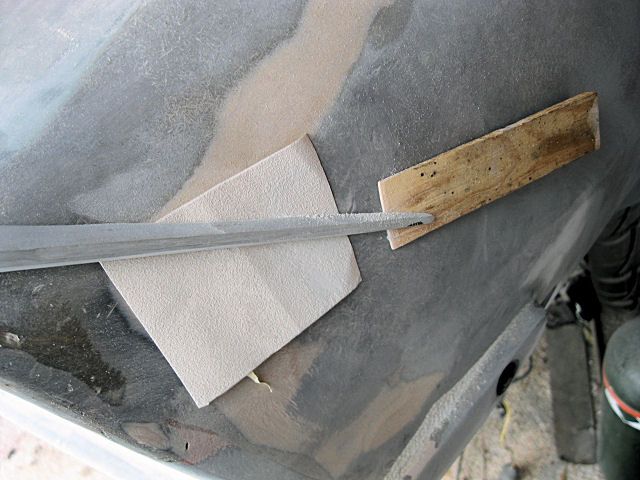
I planned to use Evercoat Vette Panel Adhesive to bond the spoiler to the body. I purchased a quart about two years ago for another part on the car but got sidetracked. The cream hardener tube split open at some point but that was no big deal – the hardener needs to be fresh – so I ordered a new tube. Before I experienced a failure with the spoiler, I wanted to test the Evercoat on that other part. It’s a speaker enclosure for the 4”x10” rear speakers I wanted to mount on the back wall of the passenger compartment. A sane person builds an enclosure and slides it into the back of the car but I make no claim to being sane.
I mixed up a batch of Evercoat. The instructions are very specific on the mix ratio (2% by weight) but obviously I exceeded that amount because it kicked off in less than 10 minutes and had no adhesive quality left. I scraped off the adhesive and decided it was too risky to use on the spoiler. I bit the bullet and bought a professional grade adhesive, gun and a bunch of extra nozzles. For a couple of reasons I chose Lord Fusor SMC Repair Adhesive (Slow) - T21 and their gun along with an extra dozen mixing nozzles. I’ve spent more than $150 just for the adhesive to attach the spoiler. It’ll be worth it if the spoiler is bonded securely to the car.
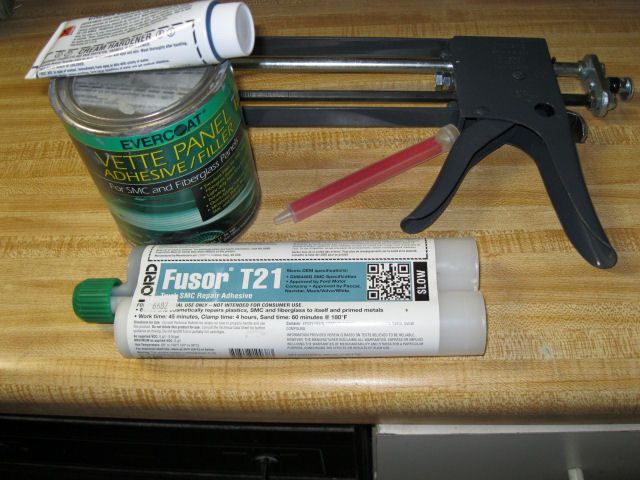
This trial and error process sucks up a lot of time. Between the cream hardener and the Lord Fusor, two weeks passed with no progress. About the time the Lord Fusor arrived, the monsoon season arrived in Florida as well. Good by April and hello May.
I drilled out the pop rivets that were holding the spoiler pieces in place. With the spoiler out of the way I drilled two holes in the rear deck under the area where the spoiler mounts. Hopefully these 9/16” holes will prevent pressure from building inside the cavity between the body and spoiler. I pictured the spoiler swelling and then exploding off the car on a hot day if there were no vents.
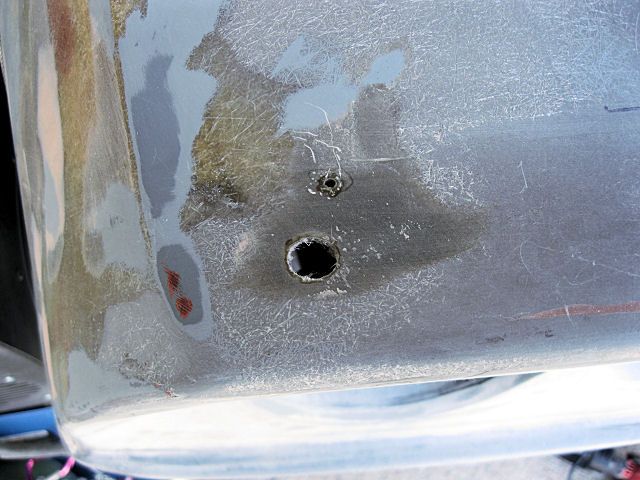
I cleaned the spoiler and deck with some really good water-based wax and grease remover and gave it an hour to dry. I didn’t take any pictures of the spoiler gluing process because I was afraid of touching things while working with the adhesive.
While I was waiting for the remover to evaporate, I hot glued the two speaker enclosures in place and applied the adhesive to the perimeter, spreading it into the gaps. It doesn’t look like much but I put quite a few hours into their construction. I have a huge soft-sided suitcase that fits perfectly into the back of the Vette so keeping the speakers out of that space was important to me.
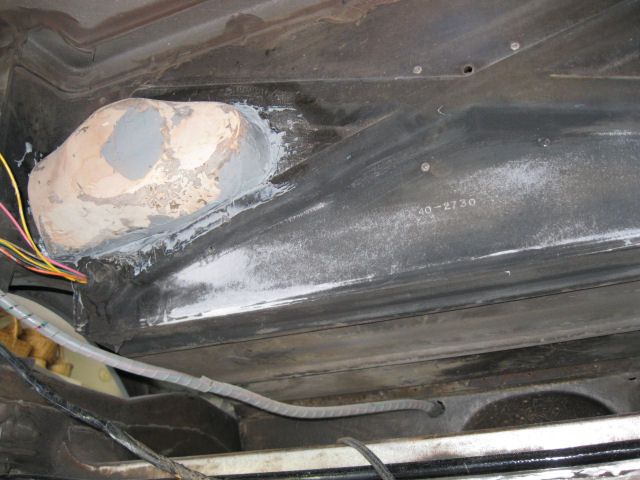
With the test completed, I applied adhesive to the spoiler flange and pop riveted the center section back in place. I pressed the spoiler down until adhesive came out along its entire length. I then applied adhesive to the vertical joint on the center section of the spoiler as well as the flange on the side pieces, one at a time. When everything was firmly attached, I cleaned up most of the excess adhesive with scrapers and some lacquer thinner soaked paper towels.
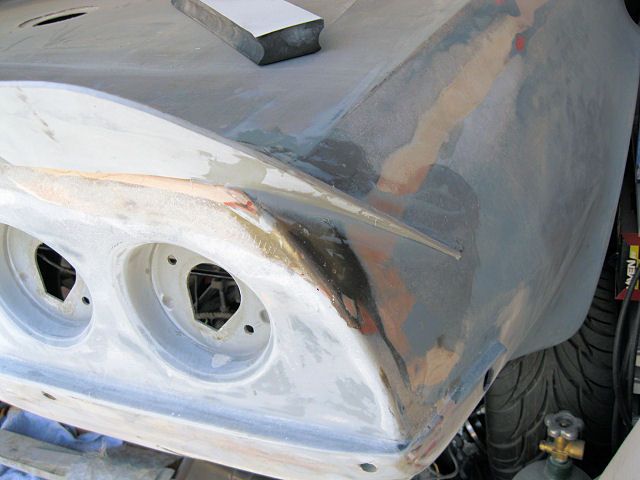
I quit working on the car and put my stuff away.
Once I had the side sections of the spoiler pop riveted in place, I did the final fitting of the legs on the sides. Not sure it was the best way to improve the fit but it seems to have worked. I put a small wedge under the leg and slid a piece of 80-grit sandpaper into the gap. This is PSA (pressure sensitive adhesive) backed paper so it has a slippery backing sheet. It took a while but when I was done the wedge was no longer needed and the paper moved reasonably well (it still dragged but I could move it with no trouble).
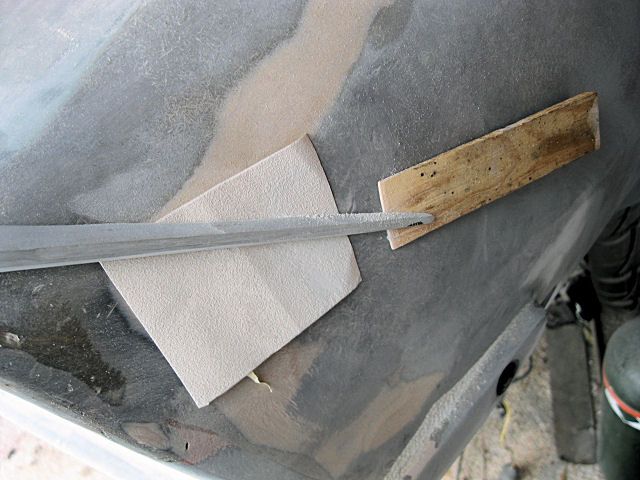
I planned to use Evercoat Vette Panel Adhesive to bond the spoiler to the body. I purchased a quart about two years ago for another part on the car but got sidetracked. The cream hardener tube split open at some point but that was no big deal – the hardener needs to be fresh – so I ordered a new tube. Before I experienced a failure with the spoiler, I wanted to test the Evercoat on that other part. It’s a speaker enclosure for the 4”x10” rear speakers I wanted to mount on the back wall of the passenger compartment. A sane person builds an enclosure and slides it into the back of the car but I make no claim to being sane.
I mixed up a batch of Evercoat. The instructions are very specific on the mix ratio (2% by weight) but obviously I exceeded that amount because it kicked off in less than 10 minutes and had no adhesive quality left. I scraped off the adhesive and decided it was too risky to use on the spoiler. I bit the bullet and bought a professional grade adhesive, gun and a bunch of extra nozzles. For a couple of reasons I chose Lord Fusor SMC Repair Adhesive (Slow) - T21 and their gun along with an extra dozen mixing nozzles. I’ve spent more than $150 just for the adhesive to attach the spoiler. It’ll be worth it if the spoiler is bonded securely to the car.
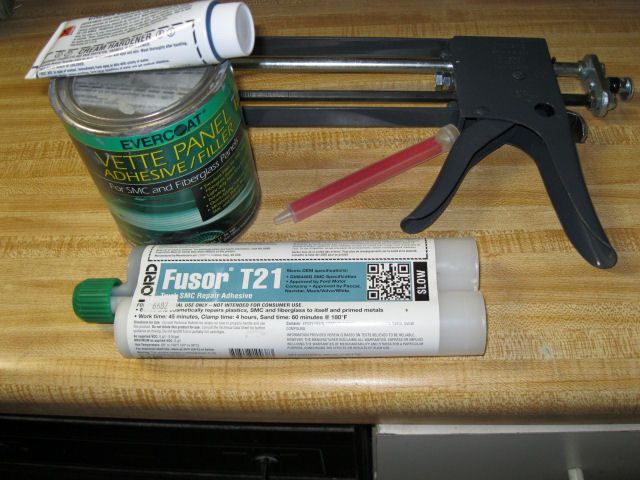
This trial and error process sucks up a lot of time. Between the cream hardener and the Lord Fusor, two weeks passed with no progress. About the time the Lord Fusor arrived, the monsoon season arrived in Florida as well. Good by April and hello May.
I drilled out the pop rivets that were holding the spoiler pieces in place. With the spoiler out of the way I drilled two holes in the rear deck under the area where the spoiler mounts. Hopefully these 9/16” holes will prevent pressure from building inside the cavity between the body and spoiler. I pictured the spoiler swelling and then exploding off the car on a hot day if there were no vents.
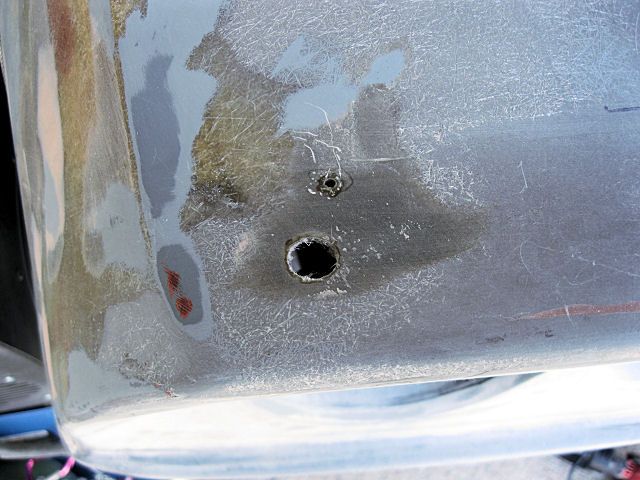
I cleaned the spoiler and deck with some really good water-based wax and grease remover and gave it an hour to dry. I didn’t take any pictures of the spoiler gluing process because I was afraid of touching things while working with the adhesive.
While I was waiting for the remover to evaporate, I hot glued the two speaker enclosures in place and applied the adhesive to the perimeter, spreading it into the gaps. It doesn’t look like much but I put quite a few hours into their construction. I have a huge soft-sided suitcase that fits perfectly into the back of the Vette so keeping the speakers out of that space was important to me.
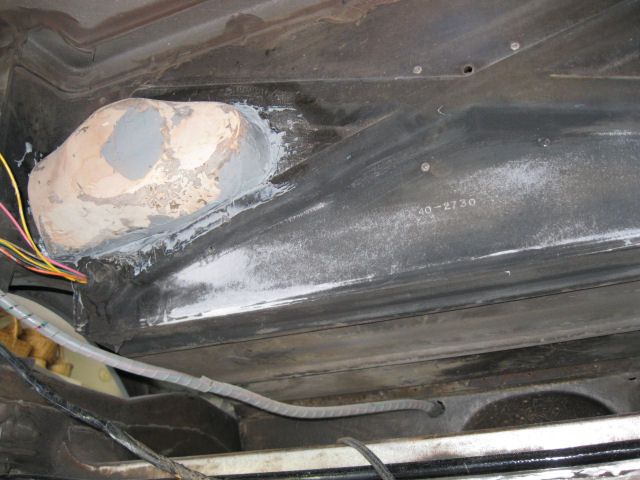
With the test completed, I applied adhesive to the spoiler flange and pop riveted the center section back in place. I pressed the spoiler down until adhesive came out along its entire length. I then applied adhesive to the vertical joint on the center section of the spoiler as well as the flange on the side pieces, one at a time. When everything was firmly attached, I cleaned up most of the excess adhesive with scrapers and some lacquer thinner soaked paper towels.
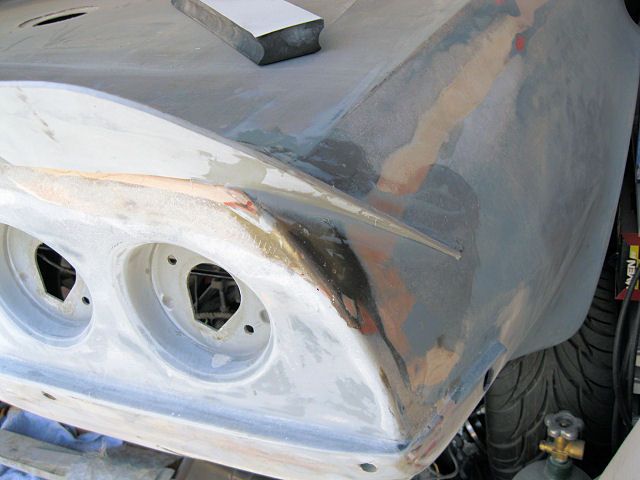
I quit working on the car and put my stuff away.
#84
Pro


Thread Starter

I’m not sure when it happened but I managed to lay a nice bead of Lord Fusor adhesive on the fender of my ’87. I didn’t notice it when it happened so it had a full 24 hours to harden up. I’ve gotta say, this stuff really sticks – to paint and whatever else it touches.
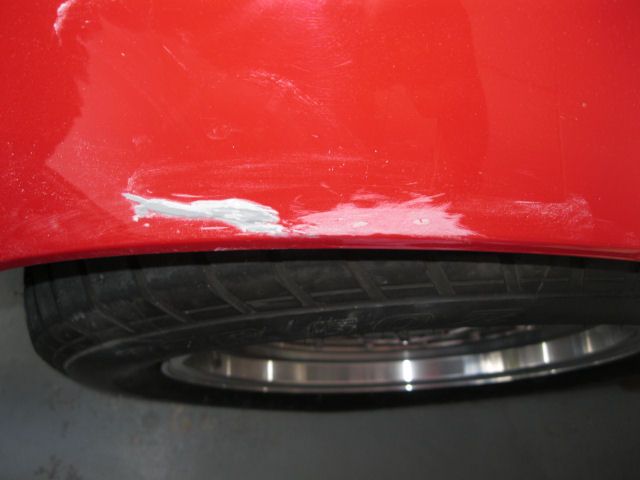
The same time I discovered this mess it started raining so an otherwise lost chunk of time got filled. I started sanding with 400-grit but the thick gob on the left was certainly going to end with me cutting through the clearcoat and make a disaster even bigger. A pro told me the safest way to remove runs was to put a piece of blue tape over the run and sand through the tape. It protects the low areas so you just cut the high spots off. I taped the area around the blob and used a small block with the sandpaper stuck to it to take off the vast majority of the adhesive.
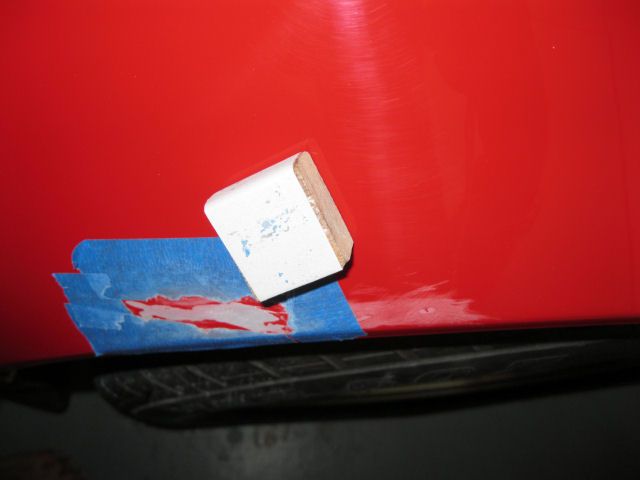
I switched to 600 wet and when the adhesive was almost transparent, I removed the tape and moved up through 800, 1000, 1500 and finally 3000 Trizact foam. I probably should have used 1200 and 2500 steps as well but I don’t seem to have any of those grits lying around. I finished it off with fine and ultra-fine compounds using my buffer on slow speed, followed by the D/A polisher with some swirl-remover for the final step.
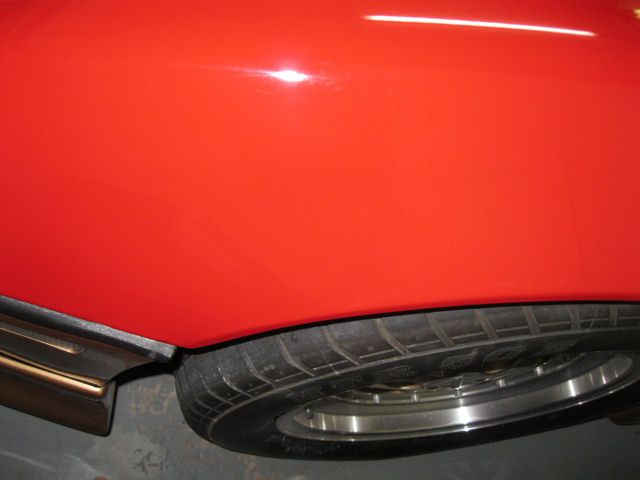
And now, back to my regularly scheduled program...
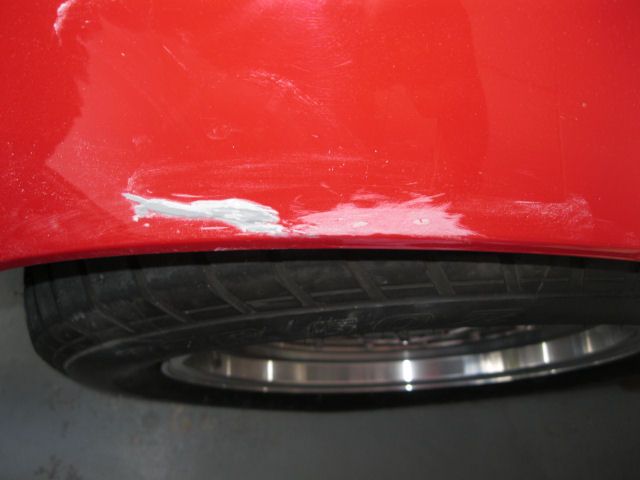
The same time I discovered this mess it started raining so an otherwise lost chunk of time got filled. I started sanding with 400-grit but the thick gob on the left was certainly going to end with me cutting through the clearcoat and make a disaster even bigger. A pro told me the safest way to remove runs was to put a piece of blue tape over the run and sand through the tape. It protects the low areas so you just cut the high spots off. I taped the area around the blob and used a small block with the sandpaper stuck to it to take off the vast majority of the adhesive.
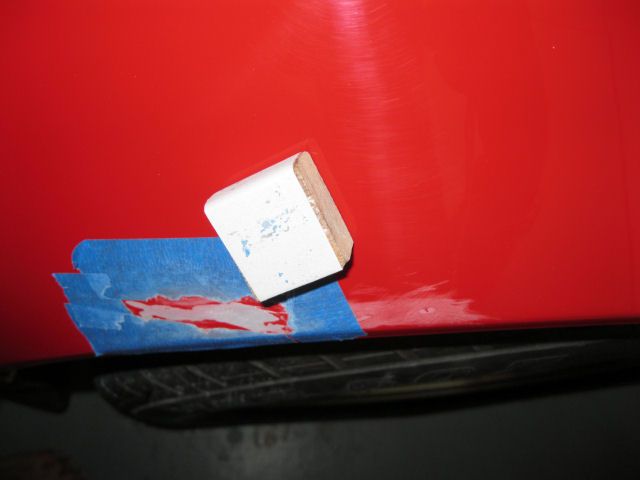
I switched to 600 wet and when the adhesive was almost transparent, I removed the tape and moved up through 800, 1000, 1500 and finally 3000 Trizact foam. I probably should have used 1200 and 2500 steps as well but I don’t seem to have any of those grits lying around. I finished it off with fine and ultra-fine compounds using my buffer on slow speed, followed by the D/A polisher with some swirl-remover for the final step.
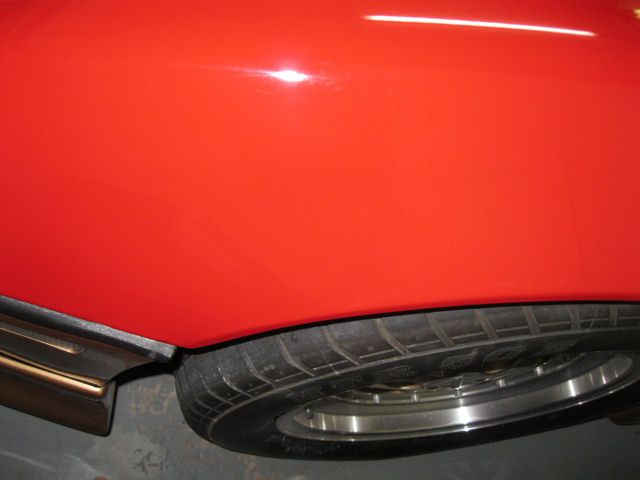
And now, back to my regularly scheduled program...
#85
Pro


Thread Starter

After our deluge let up, I opened the garage and checked the spoiler to see how solid it was. I’m not sure but it feels like the spoiler will break before the adhesive gives up. It was time to fill the gap between the spoiler and the rear panel. That gap is about two inches by four feet and I’d like to fill it with one piece of fiberglass. I rolled a four-foot piece of wax paper out on the workbench and cut two pieces of fiberglass mat about 3”x42”. I mixed up a small batch of epoxy that should saturate at least one piece. If there’s any epoxy left over, I’ll soak the second piece.
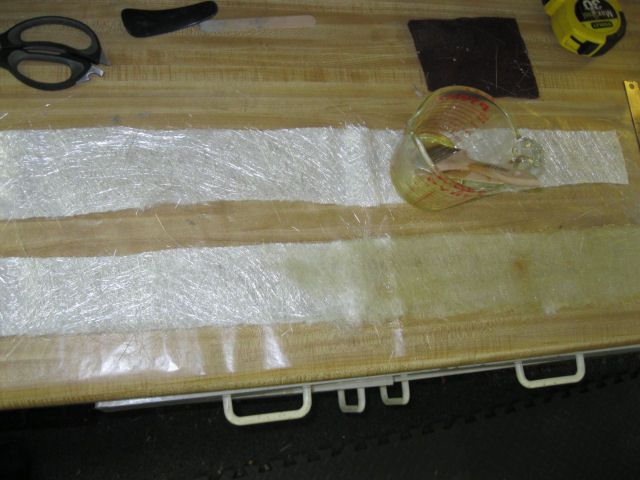
It turned out there was just enough to soak one piece so I set the second aside and transferred the strip from the bench to the car. The wax paper helps a lot because I can move and smooth the fiberglass once it’s on the car. When I work directly with the fiberglass I end up with lots of high and low spots because it sticks to my glove or whatever tool I use to work it. Working with a bigger piece of glass also seems easier with the wax paper backing. On the down side you have to be careful to remove all traces of the wax with each layer.
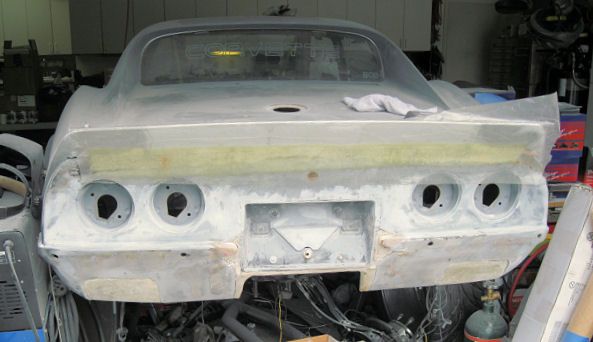
The fiberglass doesn’t cover the entire gap and it’s bigger on the left. I realized that the ends are a more complex shape and I really need to study that area before I slap fiberglass in there. The wider section will have to be ground off but that shouldn’t be a show-stopper. The hard part is going to be shaping the rear panel so it flows nicely into the spoiler. I think that’s going to be a challenge.
The coating of wax on the paper bonds with the fiberglass better than I would like. The paper doesn’t just fall off so it has to be peeled off a little at a time. As I was removing it, I also noticed a dip in the fiberglass that actually formed a large bubble. It came from the fold in the matte that you can see a couple of pictures back, right next to my epoxy mixing cup.
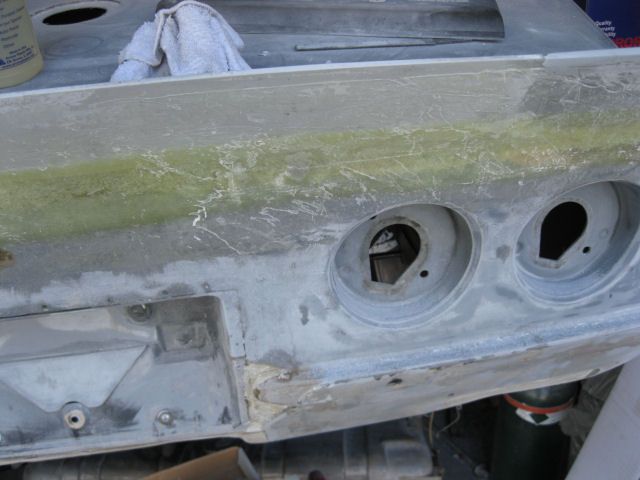
After I got the wax paper off, I washed the panel a couple of times with the wax and grease remover. Then I decided to block sand the panel a little to see how bad it’s going to be.
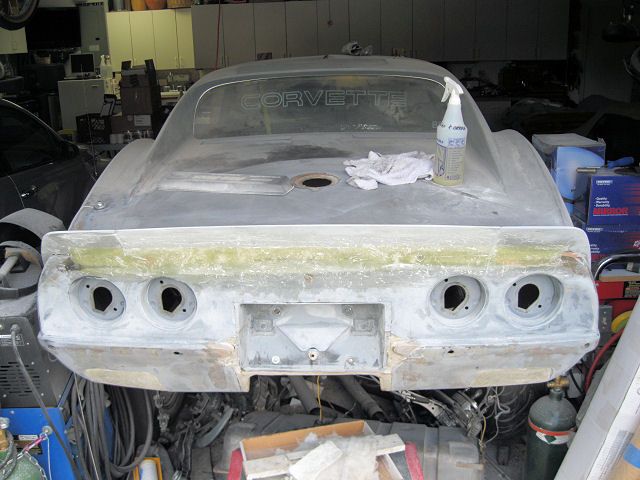
From the other side, the spoiler is looking pretty good. I plan to fill the step at the edge of the spoiler and make a smooth transition into the rear deck.
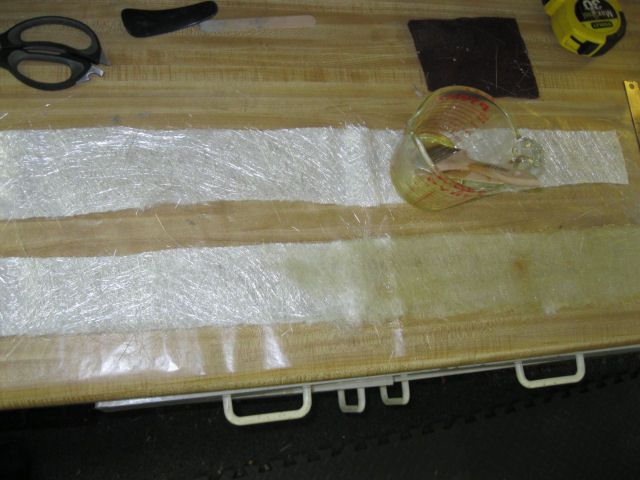
It turned out there was just enough to soak one piece so I set the second aside and transferred the strip from the bench to the car. The wax paper helps a lot because I can move and smooth the fiberglass once it’s on the car. When I work directly with the fiberglass I end up with lots of high and low spots because it sticks to my glove or whatever tool I use to work it. Working with a bigger piece of glass also seems easier with the wax paper backing. On the down side you have to be careful to remove all traces of the wax with each layer.
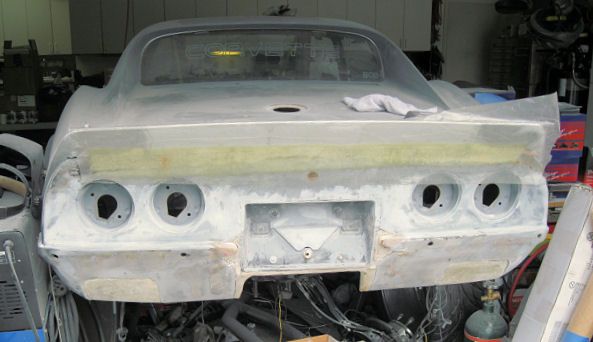
The fiberglass doesn’t cover the entire gap and it’s bigger on the left. I realized that the ends are a more complex shape and I really need to study that area before I slap fiberglass in there. The wider section will have to be ground off but that shouldn’t be a show-stopper. The hard part is going to be shaping the rear panel so it flows nicely into the spoiler. I think that’s going to be a challenge.
The coating of wax on the paper bonds with the fiberglass better than I would like. The paper doesn’t just fall off so it has to be peeled off a little at a time. As I was removing it, I also noticed a dip in the fiberglass that actually formed a large bubble. It came from the fold in the matte that you can see a couple of pictures back, right next to my epoxy mixing cup.
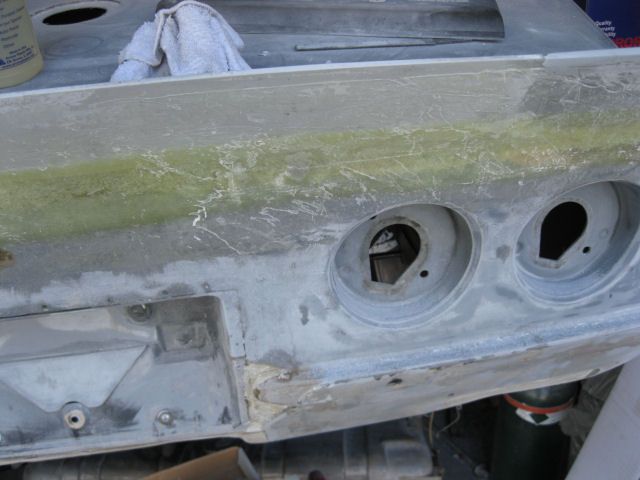
After I got the wax paper off, I washed the panel a couple of times with the wax and grease remover. Then I decided to block sand the panel a little to see how bad it’s going to be.
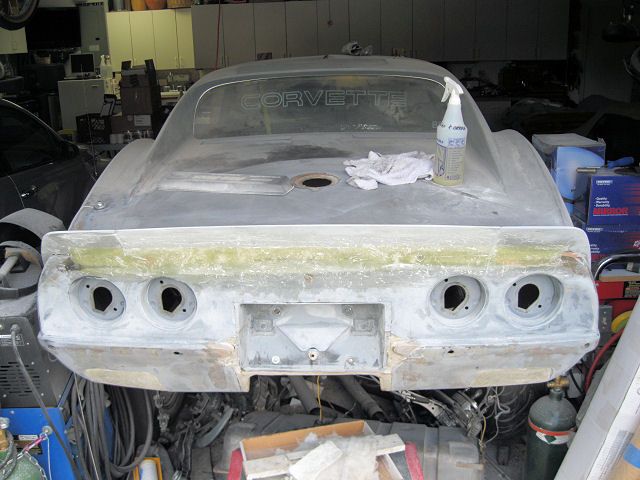
From the other side, the spoiler is looking pretty good. I plan to fill the step at the edge of the spoiler and make a smooth transition into the rear deck.
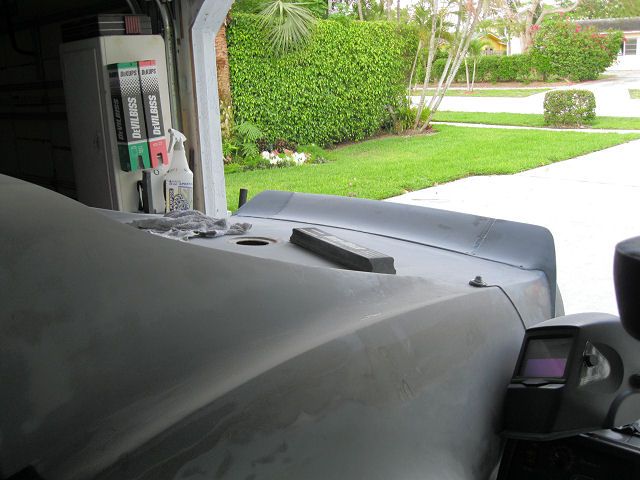
#86
Drifting



Bob, your work looks fantastic, you sure make working with fiberglass look easy. Your fiberglass instructional post will help me when I go to do the body work on my car. Thanks for the continued up dates of the great custom work you are doing with your car. I also love your ideal of recessing the speakers in the rear cargo wall.
Riggs.
Riggs.
#87
Pro


Thread Starter

Bob, your work looks fantastic, you sure make working with fiberglass look easy. Your fiberglass instructional post will help me when I go to do the body work on my car. Thanks for the continued up dates of the great custom work you are doing with your car. I also love your ideal of recessing the speakers in the rear cargo wall.
Riggs.
Riggs.
You are too kind. When I switched resin, my success rate with fiberglass work improved dramatically.
I used to buy polyester resin either from the auto supply store or a marine store. It worked OK most of the time but I had to mix a set number of drops of catalyst with a cup of resin and hope I didn't put two drops more or less than the required amount. Too little catalyst and the resin takes forever to harden. Too much catalyst and you have an inedible resin lollypop instead of a brush-full of liquid resin. Very frustrating when you mix a big batch.
A Corvette bodywork guru on another site told me about an easy-to-mix epoxy resin made by TAP plastics. You mix one part resin to one part hardener and I have yet to mess up a batch. A quart set (two pint bottles) is $35.95 plus shipping.
http://www.tapplastics.com/product/f...rpose_epoxy/28
West Marine also sells their West System with a set of calibrated pumps for the resin and catalyst. One pump of each to make a batch. It's more complicated because they offer different speed catalysts that need different ratios and therefore different pumps. Price for a quart-plus pack is $62.89 (another $15.99 for the reusable pumps) plus shipping.
http://www.westmarine.com/webapp/wcs...ts%20or%20less
#88
Drifting



Thanks for the great info, I will be installing full fender flares on all four corners of the car and was dreading the resin ratio issue, this info is greatly appereated. I played with some small fiberglass projects and it was not very fun to deal with the resin setting up to quick or not at all.
Keep up the great work.
Riggs
Keep up the great work.
Riggs
#89
Instructor


Member Since: Feb 2008
Location: Raleigh NC
Posts: 111
Likes: 0
Received 0 Likes
on
0 Posts
St. Jude Donor '13,'15,'17,'18,'22-'23


Yes Sir like Riggs said, great info.
I haven't done any significant fiberglass work since I put a scoop on my 62 so the hood would close over the dual 4 bbls and high rise manifold and that was 30 years ago! The "new" front clip and long hood should be here in a few weeks for the 68 so I will be in fiberglass up to my eyeballs! I'm starting to itch already!

#90
Race Director



West Marine also sells their West System with a set of calibrated pumps for the resin and catalyst. One pump of each to make a batch. It's more complicated because they offer different speed catalysts that need different ratios and therefore different pumps. Price for a quart-plus pack is $62.89 (another $15.99 for the reusable pumps) plus shipping.
You can get their own packaged epoxy (everyone just packages epoxy including West Systems), at least as good as West Systems for a little better price. For example their pumps are only around 3 bucks apiece.
The 3:1 mix works very well year round in our temps.
They also carry 1:1 and 5:1.
Instead of wax paper, you may want to try 4 or 6 mil visqueen, or better yet a product called "peel ply" aka "release fabric".
BTW, nice work.

#91
Pro


Thread Starter

Thanks for the great info, I will be installing full fender flares on all four corners of the car and was dreading the resin ratio issue, this info is greatly appereated. I played with some small fiberglass projects and it was not very fun to deal with the resin setting up to quick or not at all.
Keep up the great work.
Riggs
Keep up the great work.
Riggs
I envy you doing the flares. My wife is OK with me working on the car but she specifically said "No Flares!" when I told her I was doing a little fiberglass work. She knows that the flares mean new wheels and tires and I already have my second set that has not touched a public road.
I highly recommend the Fusor adhesive if you plan to bond the flares on the body.
Yes Sir like Riggs said, great info.
I haven't done any significant fiberglass work since I put a scoop on my 62 so the hood would close over the dual 4 bbls and high rise manifold and that was 30 years ago! The "new" front clip and long hood should be here in a few weeks for the 68 so I will be in fiberglass up to my eyeballs! I'm starting to itch already!

Lately I've been looking like that 'Made of Money' man in the Geico commercials. Only difference is it's fiberglass dust, not money. If you want to do a warm-up, buy some batts of fiberglass and put it in the ceiling of your garage. I think that gave me partial immunity from this project.
Since you're somewhat local, you may want to try Fiberglass Coatings on Anglers Ave just north of Stirling.
You can get their own packaged epoxy (everyone just packages epoxy including West Systems), at least as good as West Systems for a little better price. For example their pumps are only around 3 bucks apiece.
The 3:1 mix works very well year round in our temps.
They also carry 1:1 and 5:1.
Instead of wax paper, you may want to try 4 or 6 mil visqueen, or better yet a product called "peel ply" aka "release fabric".
BTW, nice work.
You can get their own packaged epoxy (everyone just packages epoxy including West Systems), at least as good as West Systems for a little better price. For example their pumps are only around 3 bucks apiece.
The 3:1 mix works very well year round in our temps.
They also carry 1:1 and 5:1.
Instead of wax paper, you may want to try 4 or 6 mil visqueen, or better yet a product called "peel ply" aka "release fabric".
BTW, nice work.

That's great information! I checked out their site and it looks like the quart pack is just over $30. I've bookmarked the site and plan to spend some serious time there. I like supporting local businesses (especially for the shorter shipping times). If anyone else is interested, here's there website:
http://www.fgci.com/default.aspx
You're right about the wax paper. I took the roll from the kitchen 25 years ago and my wife never missed it. Sorta felt an obligation to use it up... might be time to let it go.

Last edited by Bob Heine; 05-05-2013 at 12:22 PM. Reason: Forgot wesite link
#92
Race Director



I've bookmarked the site and plan to spend some serious time there. I like supporting local businesses (especially for the shorter shipping times). If anyone else is interested, here's there website:
http://www.fgci.com/default.aspx
You're right about the wax paper. I took the roll from the kitchen 25 years ago and my wife never missed it. Sorta felt an obligation to use it up... might be time to let it go.
http://www.fgci.com/default.aspx
You're right about the wax paper. I took the roll from the kitchen 25 years ago and my wife never missed it. Sorta felt an obligation to use it up... might be time to let it go.

They even have paddleboard blanks, I might try making one since my daughter got into it.
I mentioned the the alternatives, as you know, only because wax can cause problems, even if encapsulated between layers.
#94
Pro


Thread Starter

Thanks for the compliment. I've slowed down some because of the weather. It's rained here in South Florida nearly every day through June and July so most of my work has been inside with the garage doors closed and the A/C on.
Eastwood made an offer I couldn't refuse on a TIG welder. It's a DC-only machine (no aluminum) that they had on sale for $499, including shipping.
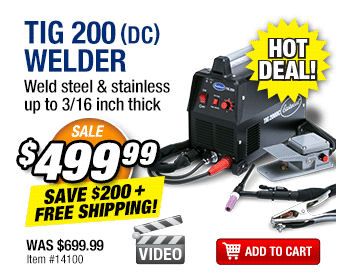
The regulator leaked when it first arrived but Eastwood sent out a replacement right away. With shipping taking a week for each modification, a month disappeared.
Now that I have 3 welders, there's no way to fit them all on one cart. Harbor Freight had their welding cart on sale and with a 20% coupon, it was delivered to the house for $35. Of course, I now need a tank of pure argon in addition to the tanks of 75/25% and 98/2% Argon/CO2. Because I'm working with stainless at the moment, the pure Argon and 98/2% tanks are going on the MIG and TIG cart. The wire welder cart will store the third tank.
While I was waiting for stuff to arrive, I got out the Eastwood MIG machine and thought I'd get some more tacks on the muffler/outlet joints. Soon as I turned on the welder, the wire started feeding and wouldn't stop until I turned the feed down to zero or turned the machine off. It was a faulty trigger switch in the gun and Eastwood Fedexed a new gun and hose assembly to me right away.
Built a wooden box to hold two 40 cu-ft tanks on the back of the new cart. Pretty sure I've exceeded it's 100 pound capacity but I'll just have to be gentle when moving the cart around.
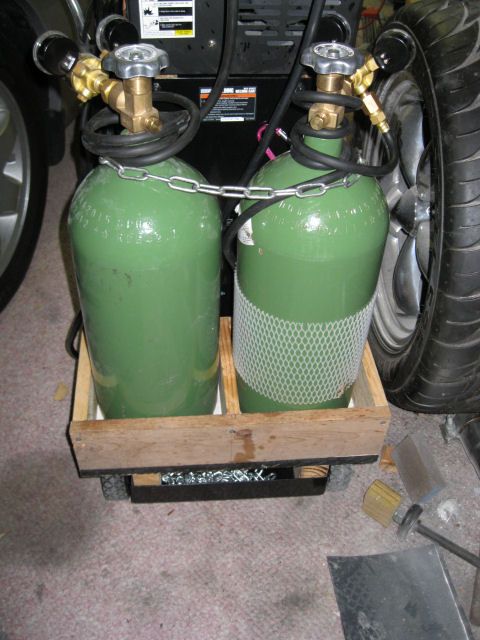
The new TIG machine is a little too big to fit on the second shelf in the welding cart so I moved the top shelf from the old blue cart to the new black cart and moved the shorter lower shelf from the black cart to the top position on the blue cart. Cut holes in the back of the new cart for the power cable, shielding gas hose and a big one for better air flow to the back of the TIG case (same size as the fan).
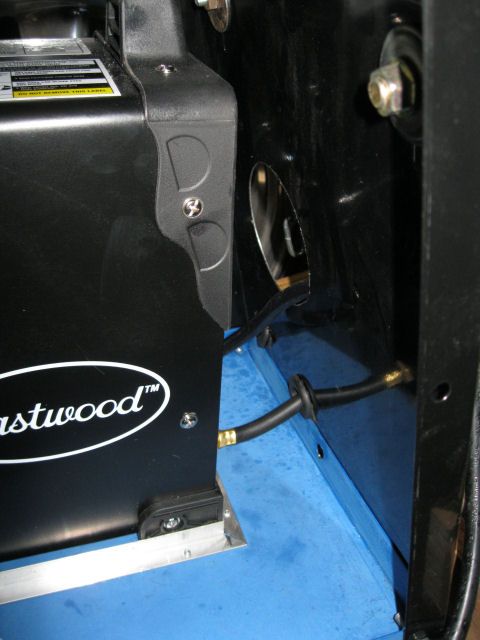
Some aluminum angle and a couple of coats of black paint on the blue shelf and wooden box and I have a new MIG and TIG cart.
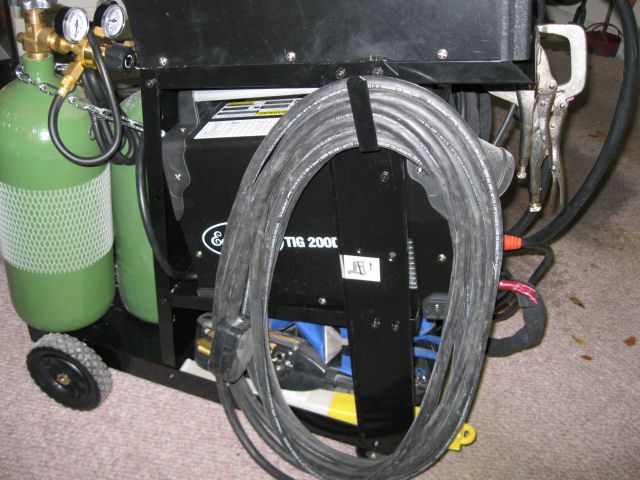
Strapped on my 40-year old artificial arm and clamped a stainless filler rod in the Farmer's Hook (very "handy" gadget for welding).
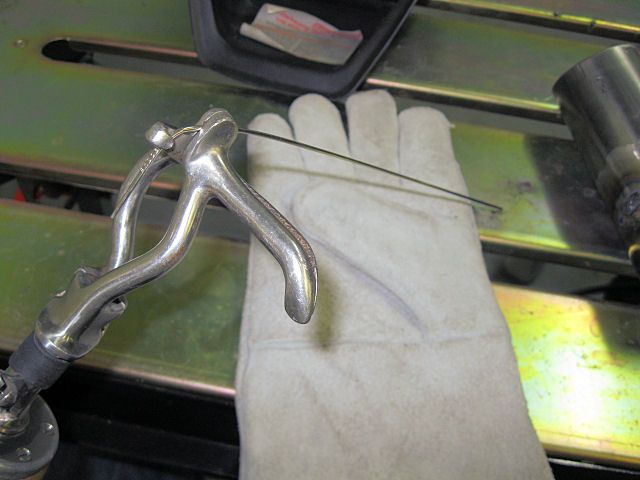
My practice scraps of stainless exhaust came together reasonably well but watching the torch and dabbing the filler rod ain't easy. I have a long way to go but it appears it's possible for me to TIG weld with one hand and an old-time hook.
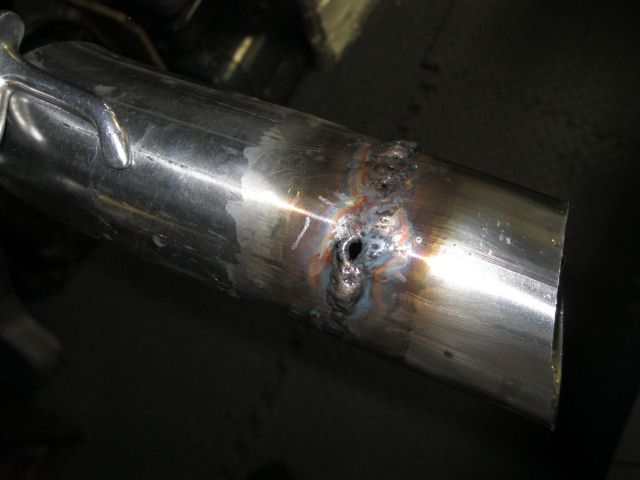
When I first tried using it, the arc seemed to be blowing around a bit so I bought a lens kit to smooth out the shielding gas flow. Also changed out the regulator for one with a sight-glass flowmeter.
I did actually work on the Corvette this summer. On one of the rare sunny days in late June, I mixed up a batch of epoxy and laid down some fiberglass on the joint between the rear deck and the spoiler. I poured the epoxy on the cloth and spread it out and everything went just great. After a couple of hours, the epoxy set up and after some sanding the next morning, I tried to repeat the process. Only thing I did different was to dip the brush into the epoxy and paint it on, instead of pouring it out of the container. Epic Fail!!! About half way across the deck, the epoxy kicked and before I could pour it out, it hardened into a perfect mess. The Pyrex cup I mixed it in was too hot to pick up and I ended up having to throw the cup away.
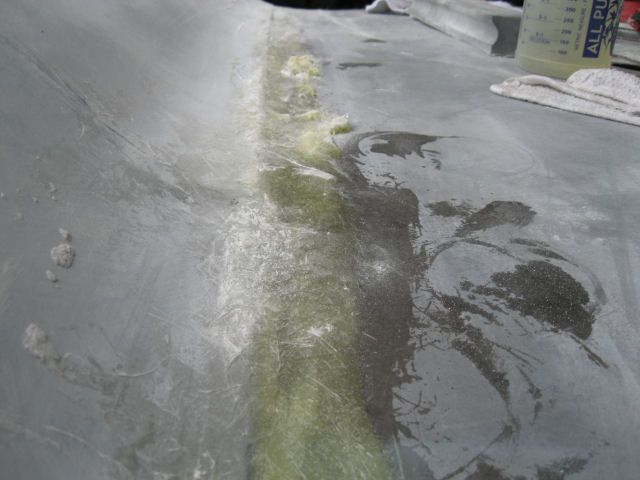
I ground off the mess and put a fresh layer of epoxy and fiberglass but in this heat (mid 80s by 9:00 in the morning) I'll just work on stuff that doesn't involve working with the garage doors open. I bought a new gas tank and in-tank fuel injection pump to get the car ready for a FAST multi-port injection setup in the near future.
Eastwood made an offer I couldn't refuse on a TIG welder. It's a DC-only machine (no aluminum) that they had on sale for $499, including shipping.
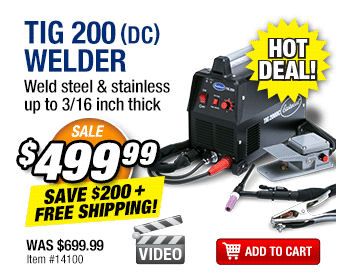
The regulator leaked when it first arrived but Eastwood sent out a replacement right away. With shipping taking a week for each modification, a month disappeared.
Now that I have 3 welders, there's no way to fit them all on one cart. Harbor Freight had their welding cart on sale and with a 20% coupon, it was delivered to the house for $35. Of course, I now need a tank of pure argon in addition to the tanks of 75/25% and 98/2% Argon/CO2. Because I'm working with stainless at the moment, the pure Argon and 98/2% tanks are going on the MIG and TIG cart. The wire welder cart will store the third tank.
While I was waiting for stuff to arrive, I got out the Eastwood MIG machine and thought I'd get some more tacks on the muffler/outlet joints. Soon as I turned on the welder, the wire started feeding and wouldn't stop until I turned the feed down to zero or turned the machine off. It was a faulty trigger switch in the gun and Eastwood Fedexed a new gun and hose assembly to me right away.
Built a wooden box to hold two 40 cu-ft tanks on the back of the new cart. Pretty sure I've exceeded it's 100 pound capacity but I'll just have to be gentle when moving the cart around.
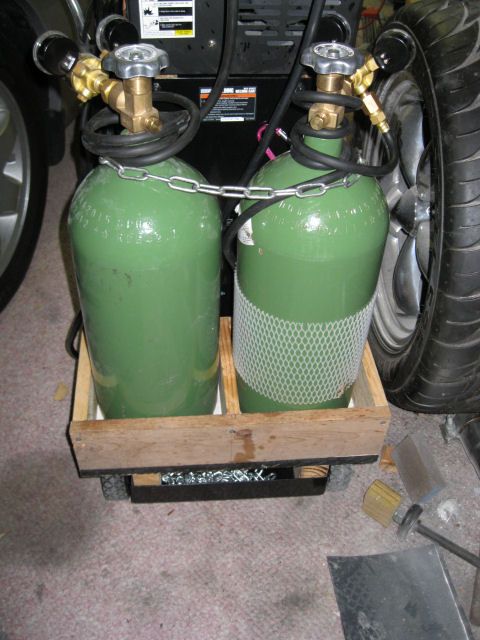
The new TIG machine is a little too big to fit on the second shelf in the welding cart so I moved the top shelf from the old blue cart to the new black cart and moved the shorter lower shelf from the black cart to the top position on the blue cart. Cut holes in the back of the new cart for the power cable, shielding gas hose and a big one for better air flow to the back of the TIG case (same size as the fan).
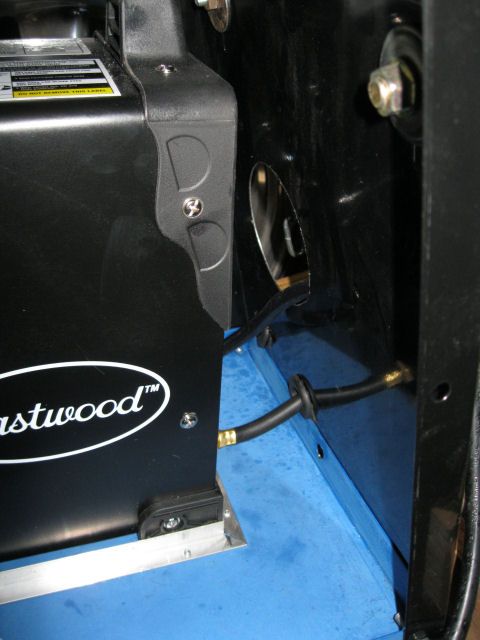
Some aluminum angle and a couple of coats of black paint on the blue shelf and wooden box and I have a new MIG and TIG cart.
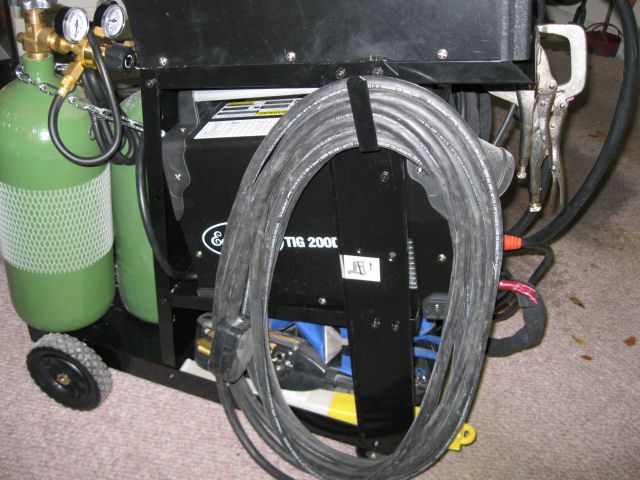
Strapped on my 40-year old artificial arm and clamped a stainless filler rod in the Farmer's Hook (very "handy" gadget for welding).
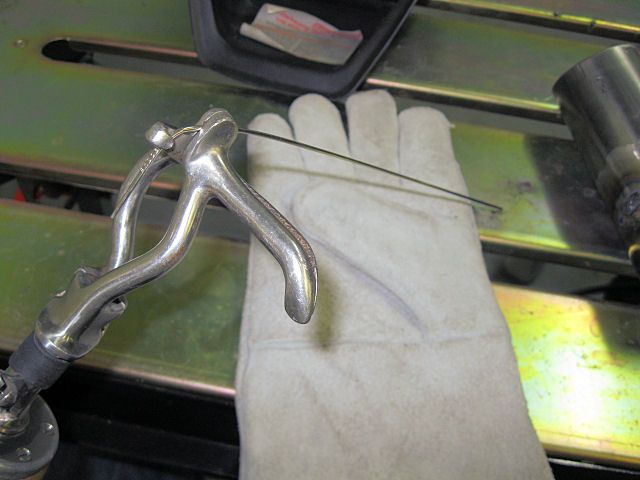
My practice scraps of stainless exhaust came together reasonably well but watching the torch and dabbing the filler rod ain't easy. I have a long way to go but it appears it's possible for me to TIG weld with one hand and an old-time hook.
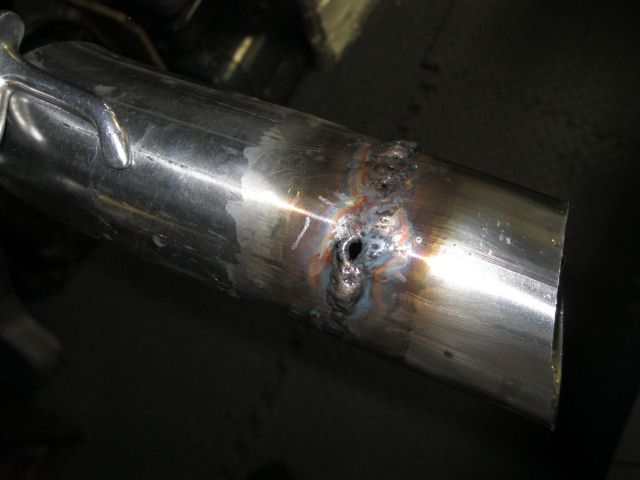
When I first tried using it, the arc seemed to be blowing around a bit so I bought a lens kit to smooth out the shielding gas flow. Also changed out the regulator for one with a sight-glass flowmeter.
I did actually work on the Corvette this summer. On one of the rare sunny days in late June, I mixed up a batch of epoxy and laid down some fiberglass on the joint between the rear deck and the spoiler. I poured the epoxy on the cloth and spread it out and everything went just great. After a couple of hours, the epoxy set up and after some sanding the next morning, I tried to repeat the process. Only thing I did different was to dip the brush into the epoxy and paint it on, instead of pouring it out of the container. Epic Fail!!! About half way across the deck, the epoxy kicked and before I could pour it out, it hardened into a perfect mess. The Pyrex cup I mixed it in was too hot to pick up and I ended up having to throw the cup away.
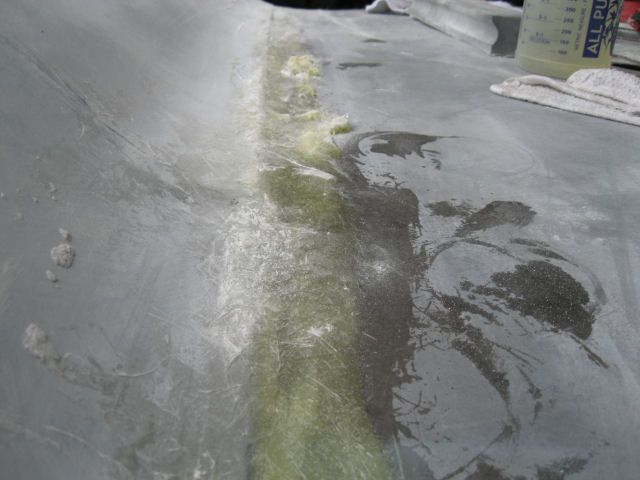
I ground off the mess and put a fresh layer of epoxy and fiberglass but in this heat (mid 80s by 9:00 in the morning) I'll just work on stuff that doesn't involve working with the garage doors open. I bought a new gas tank and in-tank fuel injection pump to get the car ready for a FAST multi-port injection setup in the near future.
#95
Burning Brakes



yes those are V-band clamps you see, they are just in front of the Deferential by a few inches. I have them also just behind the transmission cross member as well so I can take out the exhaust if needed to excess the drive line in the future.
Here are a few other older photos of the system with the v band locations, Please excuse the look of the welds, I am not a welder Nor do I pretend to be. The stainless is thin and I had trouble with the welder wanting to blow holes through the pipe until I fugued out what I was doing wrong. I used stainless so I wasn't dealing with rusty pipes later when the system has some age on it, this is not a show car by any means, Its a street car with some occasional Auto cross events mixed in.
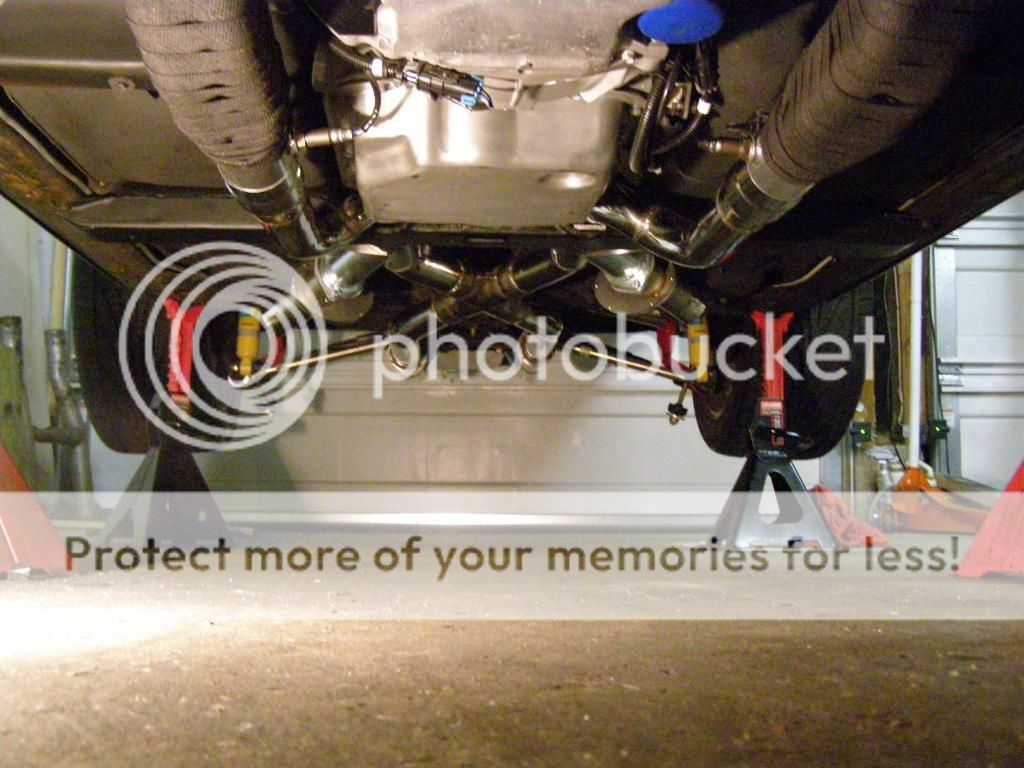


Here is a short video of the car with sound clip taken several months ago with a different set of headers and the cutouts moved closer to the floor boards along with some other changes, This will give you a decent look at the rear exhaust exit.
http://youtu.be/JxHvbqD7aOo
Riggs
Here are a few other older photos of the system with the v band locations, Please excuse the look of the welds, I am not a welder Nor do I pretend to be. The stainless is thin and I had trouble with the welder wanting to blow holes through the pipe until I fugued out what I was doing wrong. I used stainless so I wasn't dealing with rusty pipes later when the system has some age on it, this is not a show car by any means, Its a street car with some occasional Auto cross events mixed in.
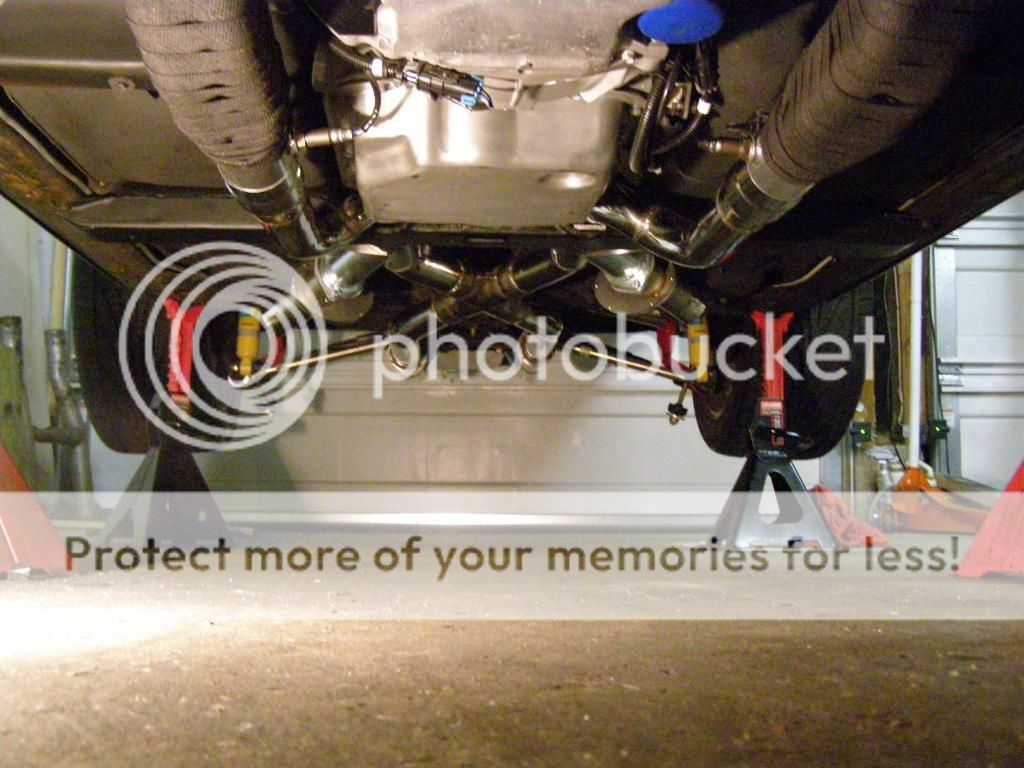


Here is a short video of the car with sound clip taken several months ago with a different set of headers and the cutouts moved closer to the floor boards along with some other changes, This will give you a decent look at the rear exhaust exit.
http://youtu.be/JxHvbqD7aOo
Riggs

#96
Le Mans Master



I have seen several C2’s with center exhaust outlets but I haven’t seen any on chrome bumper C3’s. I’m thinking of modifying my '72 coupe and decided to do it on paper first. I’d also like to get some feedback before I cut the fiberglass.
I've made several modifications to the car already so this isn’t about changing a NCRS specimen. Among the modifications is a custom rear bumper. I cut up two sets of tired old stock bumpers and had them welded up to look like a 61-62 rear bumper. I also modified the rear filler panel to remove the raised areas behind the stock bumper turn-downs. In this picture everything is loosely mounted with no time spent aligning the bumpers. The exhaust is a funky old system with quad mufflers and 1.25-inch inlet pipes. The spare tire carrier is installed in this shot:
This picture shows the new Magnaflow stainless system I bought for the car. I think the outlets look fine in the stock positions but with the spare tire carrier removed, the mufflers and pipes are really prominent. Not a real problem with the stock suspension but I'm installing the VanSteel coilover setup in the car and I would like the suspension to be visible.
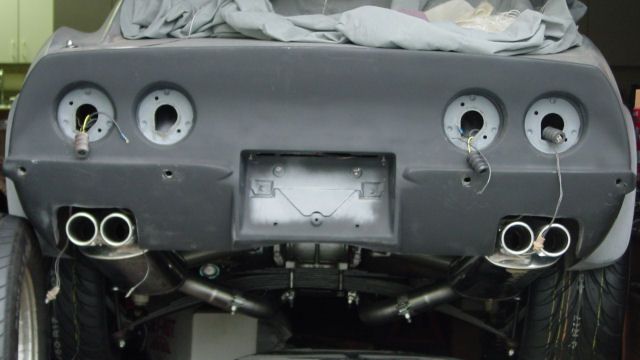
My crude photoshop of the magnaflow outlets moved to the center of the car. I also moved the license surround about 2.5 inches higher in the tail panel to position the exhaust outlets at about the same ground clearance as the stock tip location. Although this license frame location is higher than stock, it’s a lot like the frame position on a 61-62 rear.
The Magnaflow system has to be cut up a bit to fit in the new location. I will probably use the same single muffler Bee Jay used with dual 2.5-inch inlets/outlets and weld these tips on.
What do you think of the look? It's OK to hate it -- I'm way too old to have sensitive feelings -- except maybe in my feet.
I've made several modifications to the car already so this isn’t about changing a NCRS specimen. Among the modifications is a custom rear bumper. I cut up two sets of tired old stock bumpers and had them welded up to look like a 61-62 rear bumper. I also modified the rear filler panel to remove the raised areas behind the stock bumper turn-downs. In this picture everything is loosely mounted with no time spent aligning the bumpers. The exhaust is a funky old system with quad mufflers and 1.25-inch inlet pipes. The spare tire carrier is installed in this shot:
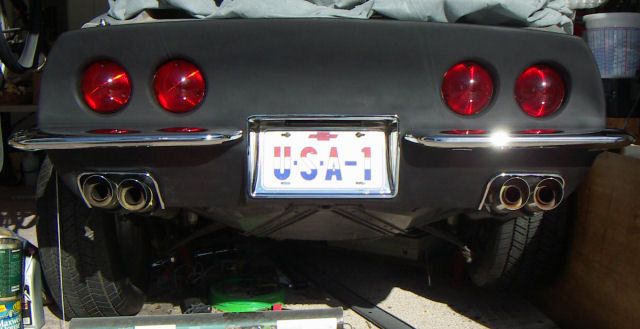
This picture shows the new Magnaflow stainless system I bought for the car. I think the outlets look fine in the stock positions but with the spare tire carrier removed, the mufflers and pipes are really prominent. Not a real problem with the stock suspension but I'm installing the VanSteel coilover setup in the car and I would like the suspension to be visible.
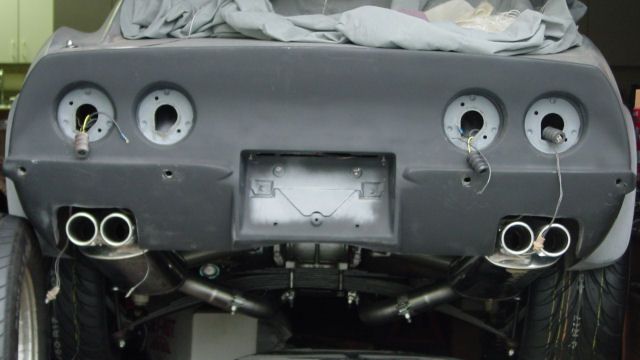
My crude photoshop of the magnaflow outlets moved to the center of the car. I also moved the license surround about 2.5 inches higher in the tail panel to position the exhaust outlets at about the same ground clearance as the stock tip location. Although this license frame location is higher than stock, it’s a lot like the frame position on a 61-62 rear.
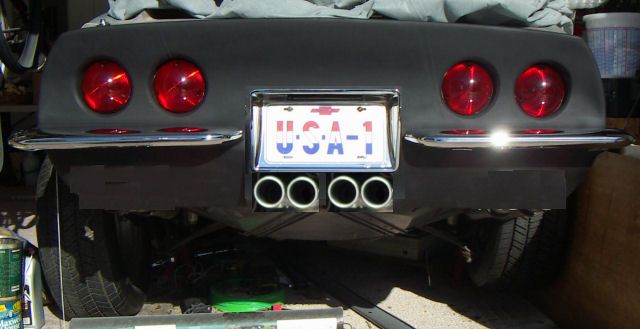
The Magnaflow system has to be cut up a bit to fit in the new location. I will probably use the same single muffler Bee Jay used with dual 2.5-inch inlets/outlets and weld these tips on.
What do you think of the look? It's OK to hate it -- I'm way too old to have sensitive feelings -- except maybe in my feet.

Last edited by TedH; 08-18-2013 at 04:08 PM.
#97
Pro


Thread Starter

I'd go with a system that removes the rear tire... how often do you really use it? But, it should look BETTER than what the car has w/out spare. Show off the IRS and the trick duals set-up. I like the idea... gets the exhaust AWAY from the tires and fewer bends once it passes under the IRS. 

At one point I was going to buy a 4-inch rallye wheel with the narrowest 27-inch tall tire on it and then section the spare tire carrier. Even before I priced the bits and pieces and estimated the work, I came to the same conclusion as you. On the miniscule chance I can't get AAA to come out and fix the flat, I can carry a tire plug kit and one of those $8 compressors under the storage bin with the scissor jack.
Since I'm also doing away with the rear leaf spring, four really nice threaded mounting bolt holes are freed up under the IRS pumpkin. I should be able to fabricate a nice exhaust hanger for that spot.
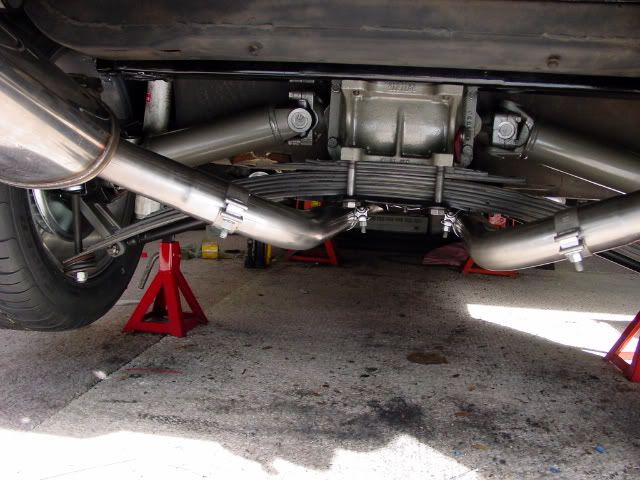
#98
Melting Slicks



Thanks for the compliment. I've slowed down some because of the weather. It's rained here in South Florida nearly every day through June and July so most of my work has been inside with the garage doors closed and the A/C on.
Eastwood made an offer I couldn't refuse on a TIG welder. It's a DC-only machine (no aluminum) that they had on sale for $499, including shipping.
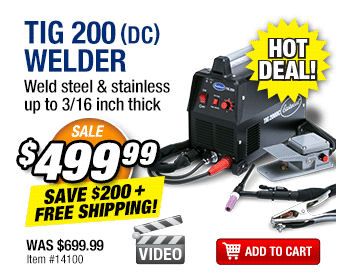
The regulator leaked when it first arrived but Eastwood sent out a replacement right away. With shipping taking a week for each modification, a month disappeared.
Now that I have 3 welders, there's no way to fit them all on one cart. Harbor Freight had their welding cart on sale and with a 20% coupon, it was delivered to the house for $35. Of course, I now need a tank of pure argon in addition to the tanks of 75/25% and 98/2% Argon/CO2. Because I'm working with stainless at the moment, the pure Argon and 98/2% tanks are going on the MIG and TIG cart. The wire welder cart will store the third tank.
While I was waiting for stuff to arrive, I got out the Eastwood MIG machine and thought I'd get some more tacks on the muffler/outlet joints. Soon as I turned on the welder, the wire started feeding and wouldn't stop until I turned the feed down to zero or turned the machine off. It was a faulty trigger switch in the gun and Eastwood Fedexed a new gun and hose assembly to me right away.
Built a wooden box to hold two 40 cu-ft tanks on the back of the new cart. Pretty sure I've exceeded it's 100 pound capacity but I'll just have to be gentle when moving the cart around.
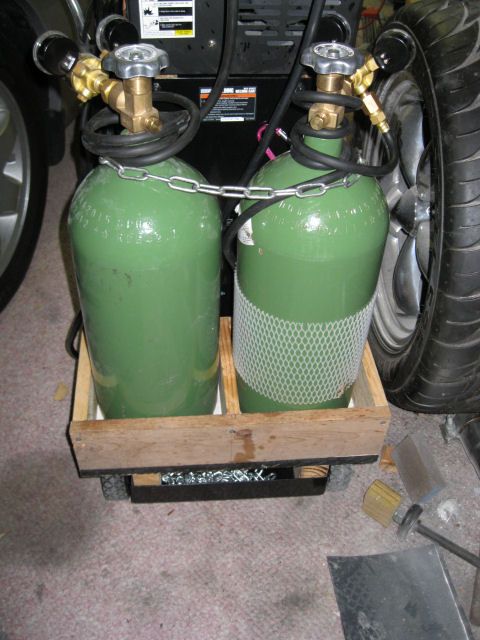
The new TIG machine is a little too big to fit on the second shelf in the welding cart so I moved the top shelf from the old blue cart to the new black cart and moved the shorter lower shelf from the black cart to the top position on the blue cart. Cut holes in the back of the new cart for the power cable, shielding gas hose and a big one for better air flow to the back of the TIG case (same size as the fan).
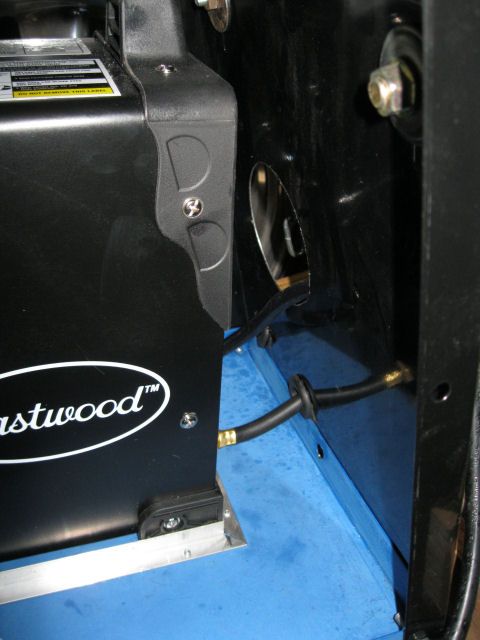
Some aluminum angle and a couple of coats of black paint on the blue shelf and wooden box and I have a new MIG and TIG cart.
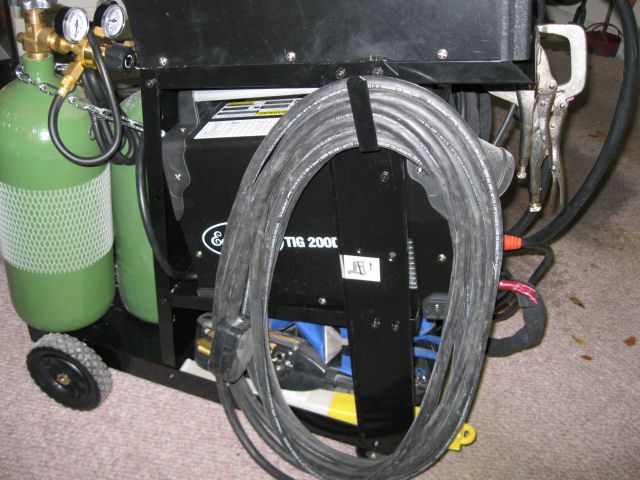
Strapped on my 40-year old artificial arm and clamped a stainless filler rod in the Farmer's Hook (very "handy" gadget for welding).
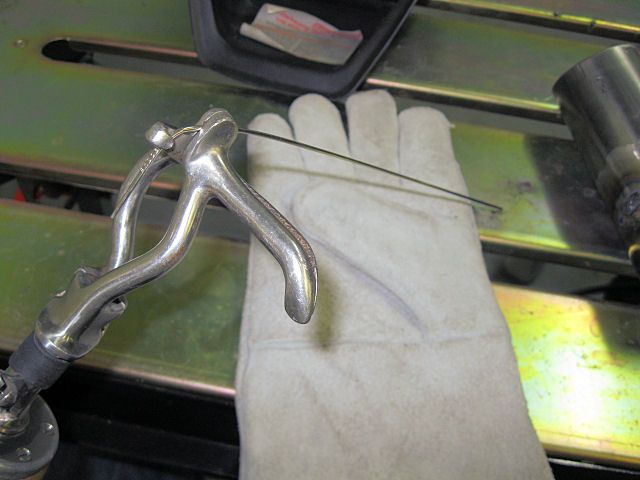
My practice scraps of stainless exhaust came together reasonably well but watching the torch and dabbing the filler rod ain't easy. I have a long way to go but it appears it's possible for me to TIG weld with one hand and an old-time hook.
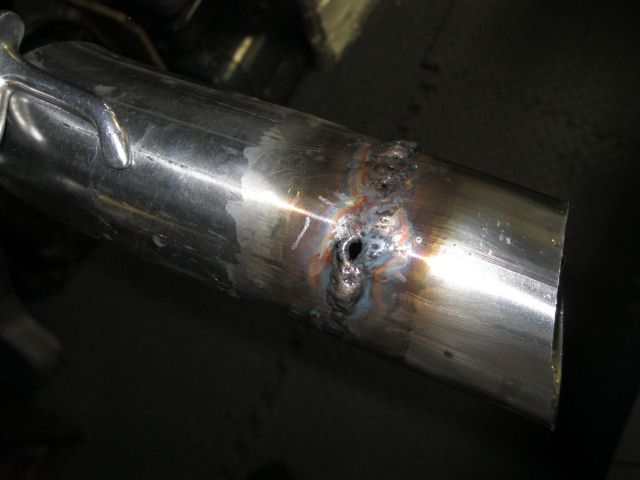
When I first tried using it, the arc seemed to be blowing around a bit so I bought a lens kit to smooth out the shielding gas flow. Also changed out the regulator for one with a sight-glass flowmeter.
I did actually work on the Corvette this summer. On one of the rare sunny days in late June, I mixed up a batch of epoxy and laid down some fiberglass on the joint between the rear deck and the spoiler. I poured the epoxy on the cloth and spread it out and everything went just great. After a couple of hours, the epoxy set up and after some sanding the next morning, I tried to repeat the process. Only thing I did different was to dip the brush into the epoxy and paint it on, instead of pouring it out of the container. Epic Fail!!! About half way across the deck, the epoxy kicked and before I could pour it out, it hardened into a perfect mess. The Pyrex cup I mixed it in was too hot to pick up and I ended up having to throw the cup away.
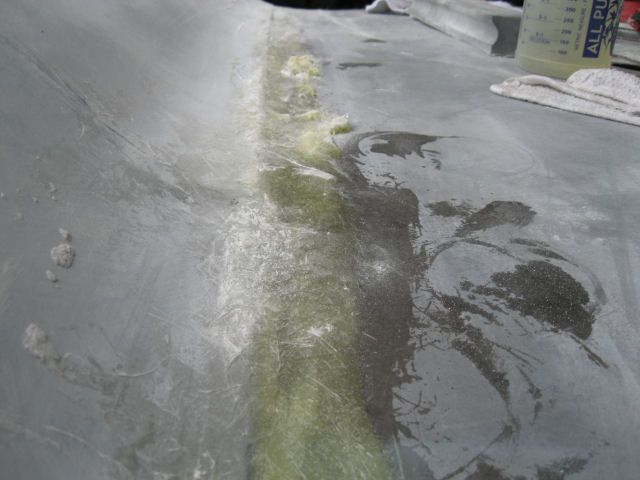
I ground off the mess and put a fresh layer of epoxy and fiberglass but in this heat (mid 80s by 9:00 in the morning) I'll just work on stuff that doesn't involve working with the garage doors open. I bought a new gas tank and in-tank fuel injection pump to get the car ready for a FAST multi-port injection setup in the near future.
Eastwood made an offer I couldn't refuse on a TIG welder. It's a DC-only machine (no aluminum) that they had on sale for $499, including shipping.
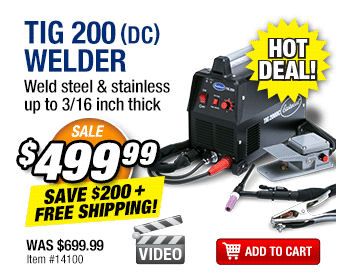
The regulator leaked when it first arrived but Eastwood sent out a replacement right away. With shipping taking a week for each modification, a month disappeared.
Now that I have 3 welders, there's no way to fit them all on one cart. Harbor Freight had their welding cart on sale and with a 20% coupon, it was delivered to the house for $35. Of course, I now need a tank of pure argon in addition to the tanks of 75/25% and 98/2% Argon/CO2. Because I'm working with stainless at the moment, the pure Argon and 98/2% tanks are going on the MIG and TIG cart. The wire welder cart will store the third tank.
While I was waiting for stuff to arrive, I got out the Eastwood MIG machine and thought I'd get some more tacks on the muffler/outlet joints. Soon as I turned on the welder, the wire started feeding and wouldn't stop until I turned the feed down to zero or turned the machine off. It was a faulty trigger switch in the gun and Eastwood Fedexed a new gun and hose assembly to me right away.
Built a wooden box to hold two 40 cu-ft tanks on the back of the new cart. Pretty sure I've exceeded it's 100 pound capacity but I'll just have to be gentle when moving the cart around.
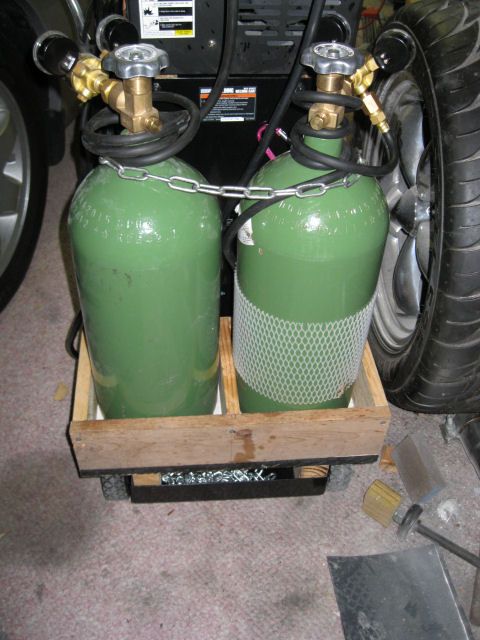
The new TIG machine is a little too big to fit on the second shelf in the welding cart so I moved the top shelf from the old blue cart to the new black cart and moved the shorter lower shelf from the black cart to the top position on the blue cart. Cut holes in the back of the new cart for the power cable, shielding gas hose and a big one for better air flow to the back of the TIG case (same size as the fan).
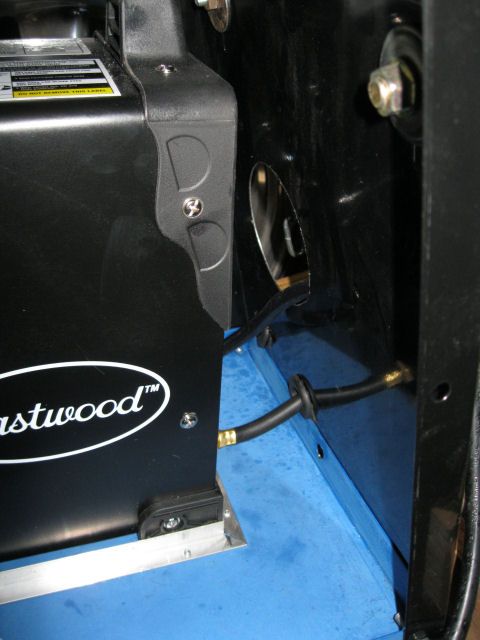
Some aluminum angle and a couple of coats of black paint on the blue shelf and wooden box and I have a new MIG and TIG cart.
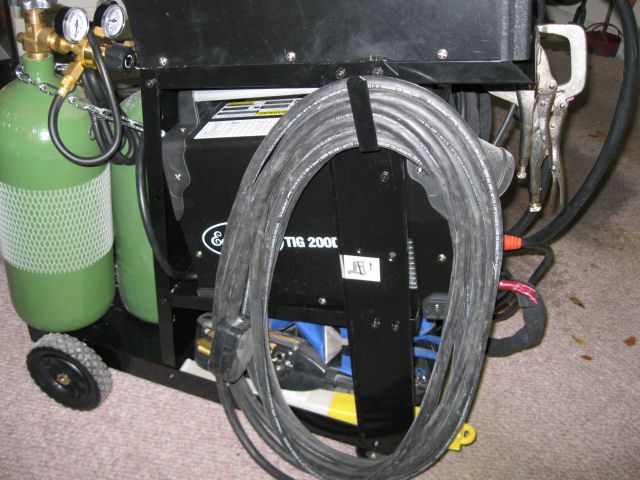
Strapped on my 40-year old artificial arm and clamped a stainless filler rod in the Farmer's Hook (very "handy" gadget for welding).
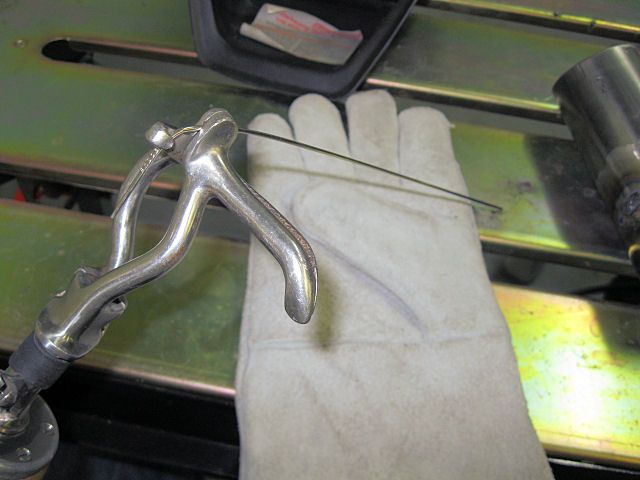
My practice scraps of stainless exhaust came together reasonably well but watching the torch and dabbing the filler rod ain't easy. I have a long way to go but it appears it's possible for me to TIG weld with one hand and an old-time hook.
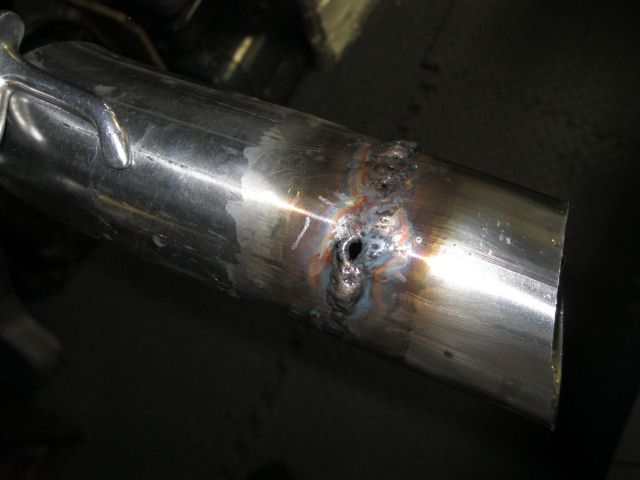
When I first tried using it, the arc seemed to be blowing around a bit so I bought a lens kit to smooth out the shielding gas flow. Also changed out the regulator for one with a sight-glass flowmeter.
I did actually work on the Corvette this summer. On one of the rare sunny days in late June, I mixed up a batch of epoxy and laid down some fiberglass on the joint between the rear deck and the spoiler. I poured the epoxy on the cloth and spread it out and everything went just great. After a couple of hours, the epoxy set up and after some sanding the next morning, I tried to repeat the process. Only thing I did different was to dip the brush into the epoxy and paint it on, instead of pouring it out of the container. Epic Fail!!! About half way across the deck, the epoxy kicked and before I could pour it out, it hardened into a perfect mess. The Pyrex cup I mixed it in was too hot to pick up and I ended up having to throw the cup away.
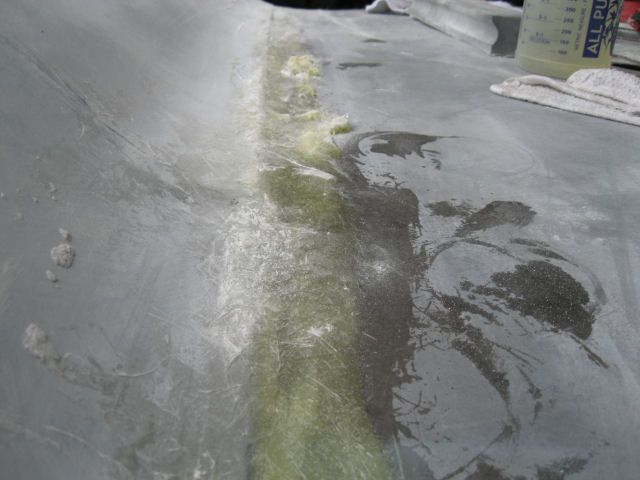
I ground off the mess and put a fresh layer of epoxy and fiberglass but in this heat (mid 80s by 9:00 in the morning) I'll just work on stuff that doesn't involve working with the garage doors open. I bought a new gas tank and in-tank fuel injection pump to get the car ready for a FAST multi-port injection setup in the near future.
#99
Pro


Thread Starter

After Tig Welding a couple of 304 SS Exhausts togeather and never getting the results I wanted I figure out why. The Air inside the Tube is polluting the Welds. They make a paste that You smear on the inside just before You weld it and it will melt into a Gas that protects it. Another way and probably the prefered way is to purdge the inside of the Tube with Argon.
#100
Melting Slicks



Thanks for the advice. I knew I should be doing something to protect the weld but making a purge gas setup appeared to be a pretty expensive solution, especially for a two-inlet, four outlet muffler, I found the company that supplies the paste and e-mailed them a request when I couldn't find a local supplier. The company I found is Superior Flux & Mfg. Co. and the flux is Superior No. 9 Welding Stainless Steel Backup Flux. I've written to them and I'll let you know how that works out.