3" or 2.5" duel exhaust (what's better?) and X-pipe
#61
Instructor


Member Since: Dec 2003
Location: Ludlow MA
Posts: 249
Likes: 0
Received 0 Likes
on
0 Posts


I am watching this thead with interest to see if anyone offers a 3" kit for the C3, or in my case C2. My case is different as I have an LT5 with headers and I'm getting ready to fab the exhaust. Would sure be nice if a 3" madrel bent system existed so that I could save some of the welding and fabrication...
#62
Drifting



I am watching this thead with interest to see if anyone offers a 3" kit for the C3, or in my case C2. My case is different as I have an LT5 with headers and I'm getting ready to fab the exhaust. Would sure be nice if a 3" madrel bent system existed so that I could save some of the welding and fabrication...
I know that I never found one.
#63
Le Mans Master



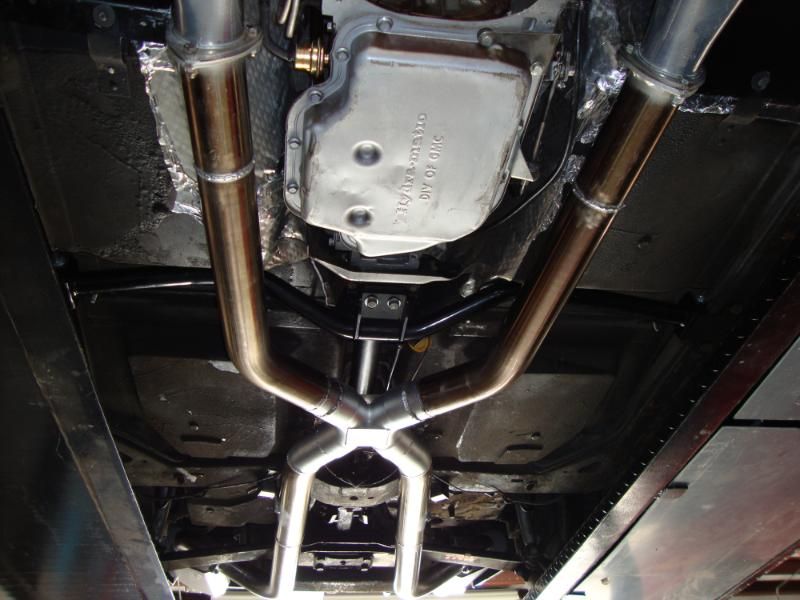
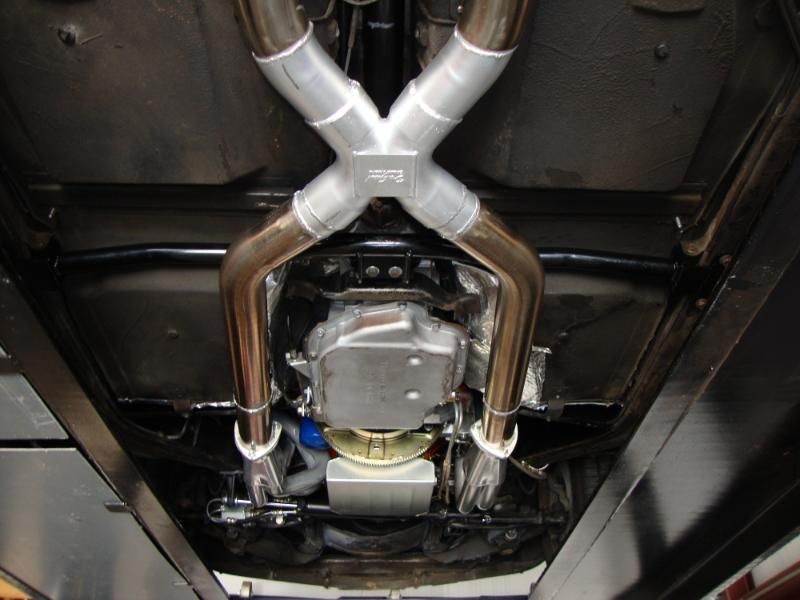
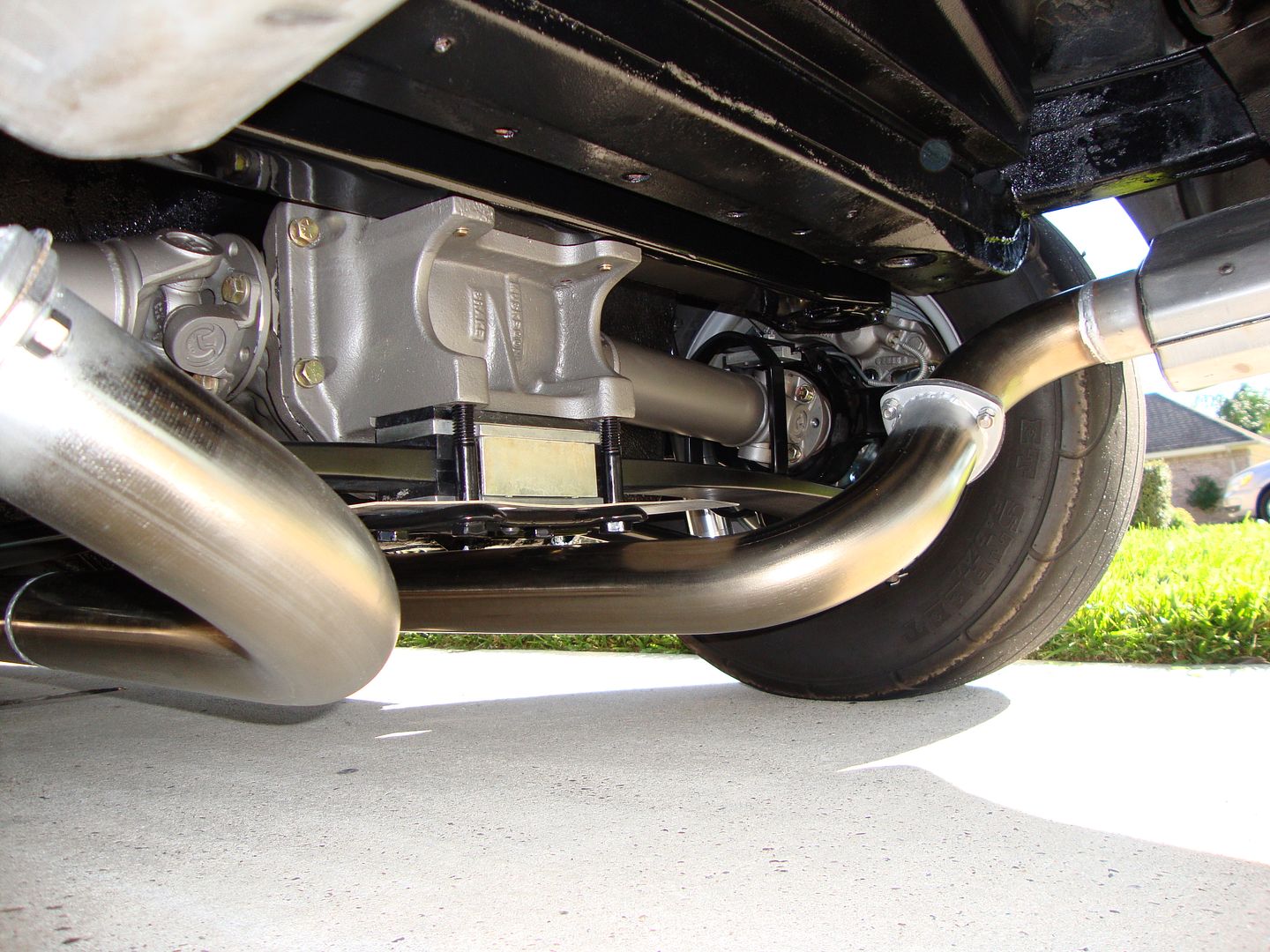
Modded the stock tips for 3" oval pipe..
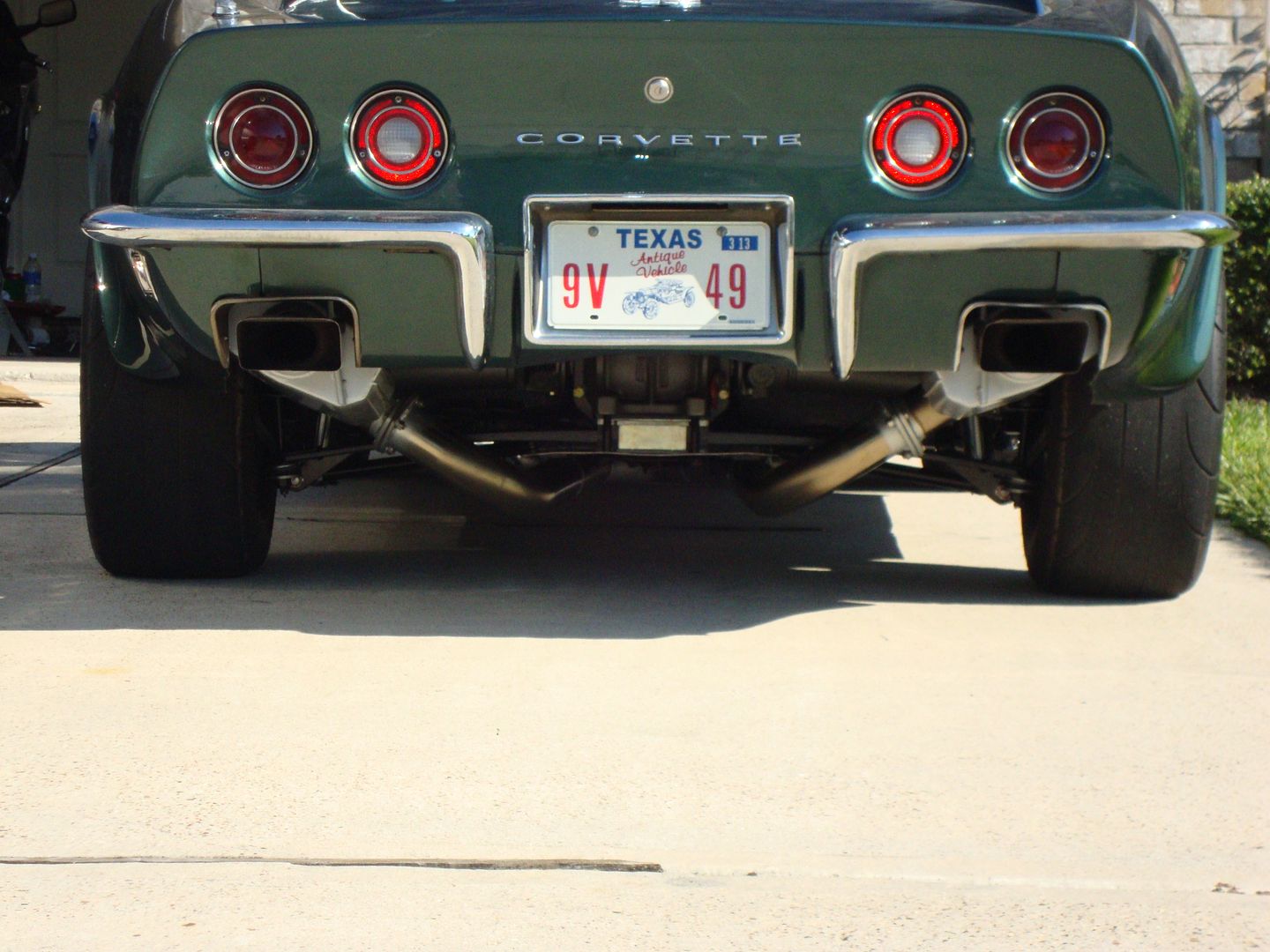
Came out pretty good I think....But I wish I could have used 3.5" pipe so I could have slowed this thing down some more....


#64

Nice
Nope...no one makes one....You will have to have it built locally or do it yourself....My local shop did this one...pieced it together from mandrel sections...
Came out pretty good I think....But I wish I could have used 3.5" pipe so I could have slowed this thing down some more....

Came out pretty good I think....But I wish I could have used 3.5" pipe so I could have slowed this thing down some more....


#65
Race Director


Thread Starter



but actually it seems there is two very strong arguments on this, conventional wisdom says bigger...... but it seems that most, if not all name brand muffler/exhaust system manufactures say different???? what does the ZR1 run i wonder? And yes, to me a 3" pipe does sound better.... but, this is why I ask the question...

#66
Race Director



Wow this guy isn't going to be very popular around here and it's from the CorvetteForum too 
Home » C6 » Engine
Share this with your friends
Chevrolet Corvette Exhaust Pipe Size
Many Chevrolet Corvette owners express this philosophy on exhaust piping size: the bigger, the better. As you will see, this is not necessarily so.
When moving exhaust gases away from your Corvette and you, the objective is to keep them hot. Why? One reason is so that they flow out of the exhaust pipe more quickly. It is matter of relative weight. The cooler air is, the denser it is, and thus the heavier it is. In a larger pipe, the gases have a longer chance to cool off. Theoretically, therefore, with larger exhaust system piping we are asking our Corvette engine to push out a larger amount of relatively cooler, heavier air.
Overly-large piping also affects header tuning. With the larger piping, exhaust pulses achieve a higher level of exhaust-gas entropy (essentially de-energized exhaust gases), which will throw off our header tuning calculations. This is because the vibrational pulses will line up differently than in a smaller pipe. Coating the exhaust system with insulation, like a ceramic thermal barrier or header wrap, will reduce this affect slightly, but this is an expensive way to go.
Realistically there is no set formula for determining piping size. It all depends on the exhaust system: how many kinks and bends, muffler configuration, exhaust gas temperature, etc. As a general rule of thumb, engines producing 250 to 350 horsepower choose 3 to 3.5 inch piping. Four hundred to 500 hp, choose 4 inch."

Home » C6 » Engine
Share this with your friends
Chevrolet Corvette Exhaust Pipe Size
Many Chevrolet Corvette owners express this philosophy on exhaust piping size: the bigger, the better. As you will see, this is not necessarily so.
When moving exhaust gases away from your Corvette and you, the objective is to keep them hot. Why? One reason is so that they flow out of the exhaust pipe more quickly. It is matter of relative weight. The cooler air is, the denser it is, and thus the heavier it is. In a larger pipe, the gases have a longer chance to cool off. Theoretically, therefore, with larger exhaust system piping we are asking our Corvette engine to push out a larger amount of relatively cooler, heavier air.
Overly-large piping also affects header tuning. With the larger piping, exhaust pulses achieve a higher level of exhaust-gas entropy (essentially de-energized exhaust gases), which will throw off our header tuning calculations. This is because the vibrational pulses will line up differently than in a smaller pipe. Coating the exhaust system with insulation, like a ceramic thermal barrier or header wrap, will reduce this affect slightly, but this is an expensive way to go.
Realistically there is no set formula for determining piping size. It all depends on the exhaust system: how many kinks and bends, muffler configuration, exhaust gas temperature, etc. As a general rule of thumb, engines producing 250 to 350 horsepower choose 3 to 3.5 inch piping. Four hundred to 500 hp, choose 4 inch."
#67

2 1/2" exhaust was used on the dyno. Now, I wasn't trying to tell YOU anything! My original post was only my opinion to Pauldana's question. This IS his thread.
Oh, if you want me to put my car on a chassis dyno and do the tests, send me a check for $800 and I'll do it! simple!
#68
Race Director


Thread Starter

As i was reading and trying to do some research myself, I cam accross this on another form... this is a cut and past...
http://www.hotrodders.com/forum/exha...ula-49188.html
interesting, ......

1bad80 sent me this in a PM... I thought it'd be helpful for other sheeple here.
exhaust
Exhaust Design Comments:
The concept that maximum power is obtained by zero pressure in the exhaust is only partially true. There should be absolutely
no back-pressure from the collector rearward, but the diameter of the system beginning with the exhaust valve is a compromise. The highest efficiency for the system requires a minimum speed for good exhaust gas velocity to insure that
gas does not "back up" into the chamber during overlap at low engine speeds, and that the "suction" (negative pressure pulse) effect of a resonant (tuned length) and/or collector (overlapping exhaust pulses) system is optimized.
To predict what primary size will be best for a specific motor, you must know where you want the engine to develop peak torque. If the existing torque peak is at bit lower RPM than you prefer (typical in under-cammed or stock motors), it can be "bumped" a bit by increasing the primary diameter. If the torque peak is too high (motor is "peaky", with no range and poor recovery from
gear changes), the peak can be adjusted down by using a smaller pipe. A change of 1/8" in the primary diameter will raise or lower the peak torque RPM by 500 or so.
This factor slightly overlaps the effect of primary pipe length, but the pipe length generally will not change the peak torque or the RPM at which it occurs. A length change has the effect of improving the torque on only 1 side of the peak by "borrowing" it from the other side. A shorter pipe improves the torque after the peak (reduces it at lower RPM), preventing the curve from
flattening out so quickly as speed increases.
A longer pipe extends the torque curve backwards to improve the engine's flexibility, at the expense of after-peak torque. Less stall speed is required, and the motor will pull taller gears; this re-tunes a 4-speed motor for better operation with Torqueflite, etc.
For best effect, the gas speed in the primary tube at the peak torque RPM should be about 240 feet per second. The formula to calculate pipe size is:
Area of Primary Pipe = RPM × Cylinder Size ÷ 88,200
This determines the pipe's cross-sectional area, from which we can calculate the ID. Typical exhaust pipes are 18ga. (wall thickness of .049"), so the OD will be .098" larger. From this we can construct a formula for an 8 cylinder motor, and factor in the 18ga. wall thickness:
Area of Primary Pipe = RPM × Motor Size ÷ 705,600
Pipe ID2 = RPM × Motor Size ÷ 705,600 ÷ .7854
Pipe ID2 = RPM × Motor Size ÷ 554,177
ID = (RPM × Motor Size ÷ 554,177).5
OD = (RPM × Motor Size ÷ 554,177).5 + .098"
The following Chart shows exhaust pipe outside diameter, based on this formula, for various motor sizes and speeds. To determine if your pipe size is large enough, search across the top row for your motor size (interpolate if in between 2 sizes), and then down that column for your current pipe OD. If the peak torque RPM in the left column is high enough, your pipe is not a
restriction. If the peak torque RPM is lower than where you feel your torque peak is, look for the pipe OD on the line with your torque RPM.
If your primary pipe's wall thickness is 16ga. (.059"), add .020" to the OD figure to compensate.
LA Motors: Pipe Size @ Peak Torque RPM vs. Motor Size
Motor Size273"318"340"360"392"410"
RPMPrimary Pipe Outside Diameter, Inches
30001.311.411.451.491.551.59
32501.361.461.511.551.611.65
35001.411.521.561.611.671.71
37501.461.561.611.661.731.76
40001.501.611.661.711.781.82
42501.541.661.711.761.831.87
45001.591.701.761.811.881.92
47501.631.751.811.851.931.97
50001.671.791.851.901.982.02
52501.711.831.891.942.032.07
55001.741.871.931.992.072.12
57501.781.911.982.032.112.16
60001.821.952.022.072.162.20
Note: 392" is 340/360 block stroked with 3.79" crank; 410" is 340/360 block
stroked with 4.00" crank
B/RB Motors: Pipe Size @ Peak Torque RPM vs. Motor Size
Motor Size383"400"426"440"451"494"
RPMPrimary Pipe Outside Diameter, Inches
30001.541.571.621.641.661.73
32501.601.631.681.701.721.80
35001.651.691.741.771.791.86
37501.711.741.801.821.841.93
40001.761.801.851.881.901.99
42501.811.851.911.931.962.04
45001.861.901.961.992.012.10
47501.911.952.012.042.062.16
50001.962.002.062.092.122.21
52502.002.042.112.142.172.26
55002.052.092.152.192.212.31
57502.092.142.202.232.262.36
60002.132.182.252.282.312.41
Note: 451" is 400 block stroked with 440 crank; 494" is 400/440 block stroker
with 4.15" crank
Remember that your peak torque RPM will always be lower than your peak HP
RPM. The separation between peak torque and peak power is roughly
proportionate to your range of useable power (wider is better). Be realistic in your
estimates and plans - peak torque @ 7000 RPM sounds good, but is almost certainly
beyond the breathing ability of even a professionally-built race motor, and if
true will make the car impossible to launch. Note that 1-1/2" pipe is large
enough for a 273" motor with max torque @ 4000 RPM. A 360" only needs 1-3/4"
for 4200 RPM. A 440" is fine @ 4500 RPM with 2" primaries.
If choosing pipes for a 4WD, van, towing, etc. keep the size small to
improve torque where you need it most - the lower RPM ranges, typically 2500-3500.
One exception where use of a larger pipe (than indicated by the above
formula) will help power is, of course, motors using nitrous oxide, supercharger
or turbocharger. In these cases, size the pipe for the expected peak torque,
not the motor size.
Another instance where a slightly larger pipe may help is where the
departure angle of the pipe from the flange is very sharp (typically downward). The
added cross-sectional area immediately after the flange apparently helps
reduce the restrictive effect of a small radius after the port. This partially
explains why some header models or brands work better than others with similar
dimensions.
Minor Improvements
If possible, slightly enlarge the inside of the flange opening in the
header itself to produce a sharp step (be careful of grinding off the tube weld).
Do not radius the edge. A 1/16" bevel is generally possible and will help. If
there is not much room, don't grind all the way into the flange - a 45° angle
is fine. This has a minor anti-reversion effect, helping to prevent back-flow
at low engine speeds; helps clean up idle quality, etc.
If the primary pipe inside diameter is more than 1/8" larger than the
actual port opening in the head, the header flange bolt pattern can be slotted
slightly to raise the centerline of the primary pipe above the center of the
port, until the bottom of the pipe just matches. This puts the pipe's effective
center closer to the most active area of gas flow, and the mis-alignment at the
roof allows the highest-pressure gas an easier path away from the port; also
adds some degree of anti-reversion.
If controlling reversion is more important than maximum port flow (e.g.
primary diameter is very large), Vizard suggests the mis-match should be at the
bottom of the port where gas flow is slowest, and therefore most likely to
reverse-flow at low engine speed.
An easy way to effect a small increase in exhaust efficiency, if space
permits, is to move the header out away from the port by 1/2" or more (using an
extra gasket and longer studs or bolts). This moves the restrictive angle
farther away from the port - every little bit helps here. It also reduces local
exhaust port temperature in the head slightly. An easy spacer is an extra header
flange or 2, but be sure that the transition from the extra flange to the
header is not restricted. The extra flange may be slightly larger than the port
opening in the head, but must not step down entering the header. Do not taper,
blend, or bevel the extra flange to act as a transition between the port and
the header.
Anti-Reversion Plate
If the header in use is substantially larger than other available choices
for the same motor (i.e., you're using 2" OD, but headers are also available
in 1-5/8", etc.), an inexpensive anti-reversion plate can be made from a bare
flange with the smaller size (1-5/8"). Do these steps in order:
» Match the extra flange openings to the exhaust ports.
» Lay it over your actual 2" header flange.
» Spray paint, mark etc. the 2" openings around the 1-5/8" openings (they
will
be concentric circles).
» Remove the marked area as shown, using ball end carbide, etc.
I would suggest the following rules for best effect:
» The extra, smaller flange be no smaller than your motor's exhaust port.
» The extra flange be at least 1/4" smaller than the header in use (if
using a
header with 2" primaries, the extra flange should be 1-3/4" maximum).
» Make sure there's enough room to move both sides of the header away
from the motor by 3/8" or so (the header flange thickness).
» You may need an extra gasket between the flanges, or sealer may do
(Vizard uses silicone here)
» Longer bolts or studs will probably be needed; remember to use sealant on
B/RB motors due to water in holes.
and more:
http://victorylibrary.com/mopar/header-tech-c.htm
http://www.bgsoflex.com/bestheader.html
http://www.hotrodders.com/forum/exha...ula-49188.html
interesting, ......


1bad80 sent me this in a PM... I thought it'd be helpful for other sheeple here.
exhaust
Exhaust Design Comments:
The concept that maximum power is obtained by zero pressure in the exhaust is only partially true. There should be absolutely
no back-pressure from the collector rearward, but the diameter of the system beginning with the exhaust valve is a compromise. The highest efficiency for the system requires a minimum speed for good exhaust gas velocity to insure that
gas does not "back up" into the chamber during overlap at low engine speeds, and that the "suction" (negative pressure pulse) effect of a resonant (tuned length) and/or collector (overlapping exhaust pulses) system is optimized.
To predict what primary size will be best for a specific motor, you must know where you want the engine to develop peak torque. If the existing torque peak is at bit lower RPM than you prefer (typical in under-cammed or stock motors), it can be "bumped" a bit by increasing the primary diameter. If the torque peak is too high (motor is "peaky", with no range and poor recovery from
gear changes), the peak can be adjusted down by using a smaller pipe. A change of 1/8" in the primary diameter will raise or lower the peak torque RPM by 500 or so.
This factor slightly overlaps the effect of primary pipe length, but the pipe length generally will not change the peak torque or the RPM at which it occurs. A length change has the effect of improving the torque on only 1 side of the peak by "borrowing" it from the other side. A shorter pipe improves the torque after the peak (reduces it at lower RPM), preventing the curve from
flattening out so quickly as speed increases.
A longer pipe extends the torque curve backwards to improve the engine's flexibility, at the expense of after-peak torque. Less stall speed is required, and the motor will pull taller gears; this re-tunes a 4-speed motor for better operation with Torqueflite, etc.
For best effect, the gas speed in the primary tube at the peak torque RPM should be about 240 feet per second. The formula to calculate pipe size is:
Area of Primary Pipe = RPM × Cylinder Size ÷ 88,200
This determines the pipe's cross-sectional area, from which we can calculate the ID. Typical exhaust pipes are 18ga. (wall thickness of .049"), so the OD will be .098" larger. From this we can construct a formula for an 8 cylinder motor, and factor in the 18ga. wall thickness:
Area of Primary Pipe = RPM × Motor Size ÷ 705,600
Pipe ID2 = RPM × Motor Size ÷ 705,600 ÷ .7854
Pipe ID2 = RPM × Motor Size ÷ 554,177
ID = (RPM × Motor Size ÷ 554,177).5
OD = (RPM × Motor Size ÷ 554,177).5 + .098"
The following Chart shows exhaust pipe outside diameter, based on this formula, for various motor sizes and speeds. To determine if your pipe size is large enough, search across the top row for your motor size (interpolate if in between 2 sizes), and then down that column for your current pipe OD. If the peak torque RPM in the left column is high enough, your pipe is not a
restriction. If the peak torque RPM is lower than where you feel your torque peak is, look for the pipe OD on the line with your torque RPM.
If your primary pipe's wall thickness is 16ga. (.059"), add .020" to the OD figure to compensate.
LA Motors: Pipe Size @ Peak Torque RPM vs. Motor Size
Motor Size273"318"340"360"392"410"
RPMPrimary Pipe Outside Diameter, Inches
30001.311.411.451.491.551.59
32501.361.461.511.551.611.65
35001.411.521.561.611.671.71
37501.461.561.611.661.731.76
40001.501.611.661.711.781.82
42501.541.661.711.761.831.87
45001.591.701.761.811.881.92
47501.631.751.811.851.931.97
50001.671.791.851.901.982.02
52501.711.831.891.942.032.07
55001.741.871.931.992.072.12
57501.781.911.982.032.112.16
60001.821.952.022.072.162.20
Note: 392" is 340/360 block stroked with 3.79" crank; 410" is 340/360 block
stroked with 4.00" crank
B/RB Motors: Pipe Size @ Peak Torque RPM vs. Motor Size
Motor Size383"400"426"440"451"494"
RPMPrimary Pipe Outside Diameter, Inches
30001.541.571.621.641.661.73
32501.601.631.681.701.721.80
35001.651.691.741.771.791.86
37501.711.741.801.821.841.93
40001.761.801.851.881.901.99
42501.811.851.911.931.962.04
45001.861.901.961.992.012.10
47501.911.952.012.042.062.16
50001.962.002.062.092.122.21
52502.002.042.112.142.172.26
55002.052.092.152.192.212.31
57502.092.142.202.232.262.36
60002.132.182.252.282.312.41
Note: 451" is 400 block stroked with 440 crank; 494" is 400/440 block stroker
with 4.15" crank
Remember that your peak torque RPM will always be lower than your peak HP
RPM. The separation between peak torque and peak power is roughly
proportionate to your range of useable power (wider is better). Be realistic in your
estimates and plans - peak torque @ 7000 RPM sounds good, but is almost certainly
beyond the breathing ability of even a professionally-built race motor, and if
true will make the car impossible to launch. Note that 1-1/2" pipe is large
enough for a 273" motor with max torque @ 4000 RPM. A 360" only needs 1-3/4"
for 4200 RPM. A 440" is fine @ 4500 RPM with 2" primaries.
If choosing pipes for a 4WD, van, towing, etc. keep the size small to
improve torque where you need it most - the lower RPM ranges, typically 2500-3500.
One exception where use of a larger pipe (than indicated by the above
formula) will help power is, of course, motors using nitrous oxide, supercharger
or turbocharger. In these cases, size the pipe for the expected peak torque,
not the motor size.
Another instance where a slightly larger pipe may help is where the
departure angle of the pipe from the flange is very sharp (typically downward). The
added cross-sectional area immediately after the flange apparently helps
reduce the restrictive effect of a small radius after the port. This partially
explains why some header models or brands work better than others with similar
dimensions.
Minor Improvements
If possible, slightly enlarge the inside of the flange opening in the
header itself to produce a sharp step (be careful of grinding off the tube weld).
Do not radius the edge. A 1/16" bevel is generally possible and will help. If
there is not much room, don't grind all the way into the flange - a 45° angle
is fine. This has a minor anti-reversion effect, helping to prevent back-flow
at low engine speeds; helps clean up idle quality, etc.
If the primary pipe inside diameter is more than 1/8" larger than the
actual port opening in the head, the header flange bolt pattern can be slotted
slightly to raise the centerline of the primary pipe above the center of the
port, until the bottom of the pipe just matches. This puts the pipe's effective
center closer to the most active area of gas flow, and the mis-alignment at the
roof allows the highest-pressure gas an easier path away from the port; also
adds some degree of anti-reversion.
If controlling reversion is more important than maximum port flow (e.g.
primary diameter is very large), Vizard suggests the mis-match should be at the
bottom of the port where gas flow is slowest, and therefore most likely to
reverse-flow at low engine speed.
An easy way to effect a small increase in exhaust efficiency, if space
permits, is to move the header out away from the port by 1/2" or more (using an
extra gasket and longer studs or bolts). This moves the restrictive angle
farther away from the port - every little bit helps here. It also reduces local
exhaust port temperature in the head slightly. An easy spacer is an extra header
flange or 2, but be sure that the transition from the extra flange to the
header is not restricted. The extra flange may be slightly larger than the port
opening in the head, but must not step down entering the header. Do not taper,
blend, or bevel the extra flange to act as a transition between the port and
the header.
Anti-Reversion Plate
If the header in use is substantially larger than other available choices
for the same motor (i.e., you're using 2" OD, but headers are also available
in 1-5/8", etc.), an inexpensive anti-reversion plate can be made from a bare
flange with the smaller size (1-5/8"). Do these steps in order:
» Match the extra flange openings to the exhaust ports.
» Lay it over your actual 2" header flange.
» Spray paint, mark etc. the 2" openings around the 1-5/8" openings (they
will
be concentric circles).
» Remove the marked area as shown, using ball end carbide, etc.
I would suggest the following rules for best effect:
» The extra, smaller flange be no smaller than your motor's exhaust port.
» The extra flange be at least 1/4" smaller than the header in use (if
using a
header with 2" primaries, the extra flange should be 1-3/4" maximum).
» Make sure there's enough room to move both sides of the header away
from the motor by 3/8" or so (the header flange thickness).
» You may need an extra gasket between the flanges, or sealer may do
(Vizard uses silicone here)
» Longer bolts or studs will probably be needed; remember to use sealant on
B/RB motors due to water in holes.
and more:
http://victorylibrary.com/mopar/header-tech-c.htm
http://www.bgsoflex.com/bestheader.html
Last edited by pauldana; 11-12-2010 at 10:40 AM.
#70
Race Director



Funny, it almost does sound like you are trying to start an argument. If you had read my post a little closer, I didn't put the car on a dyno, the engine was on an engine dyno prior to being put in the car! And a
2 1/2" exhaust was used on the dyno. Now, I wasn't trying to tell YOU anything! My original post was only my opinion to Pauldana's question. This IS his thread.
Oh, if you want me to put my car on a chassis dyno and do the tests, send me a check for $800 and I'll do it! simple!
2 1/2" exhaust was used on the dyno. Now, I wasn't trying to tell YOU anything! My original post was only my opinion to Pauldana's question. This IS his thread.
Oh, if you want me to put my car on a chassis dyno and do the tests, send me a check for $800 and I'll do it! simple!
#71
Drifting



I think most are looking for max hp/torque with there new exhaust systems. Many members here have already gone the distance and tried many different applications. I myself have mirrored many members here to get the most out of my build.
Case and point, ajrothm car runs 10.7 second ET's on pump gas with 3 inch exhaust. I think I would call that success. 427Hotrod I think runs at least 3.5 inch exhaust and he runs in the 9's ET's, again another example of success in my book. If I am not mistaken I forget the members name/handle, but he has a 67 with a 632cid engine and runs a 4 inch exhaust. (do not quote me on this) but I think his dyno results were close to 1000 hp on pump gas. I had 3 inch exhaust recently installed and I absolutely love it.... It is music to my ears and fear to most when I pull up next to other cars.
I am satisfied so far. But it is low and think I already scraped it once.... oops.. 
Good thread BTW...
Case and point, ajrothm car runs 10.7 second ET's on pump gas with 3 inch exhaust. I think I would call that success. 427Hotrod I think runs at least 3.5 inch exhaust and he runs in the 9's ET's, again another example of success in my book. If I am not mistaken I forget the members name/handle, but he has a 67 with a 632cid engine and runs a 4 inch exhaust. (do not quote me on this) but I think his dyno results were close to 1000 hp on pump gas. I had 3 inch exhaust recently installed and I absolutely love it.... It is music to my ears and fear to most when I pull up next to other cars.


Good thread BTW...
#72
Race Director



Is he not saying all are pipes are too small
or maybe just mine
He has a few things I don't agree with however, according to him, my useable power is only 1500RPM but I run all day with a power range anywhere from 1700RPM to 7500RPM
"Remember that your peak torque RPM will always be lower than your peak HP RPM. The separation between peak torque and peak power is roughly proportionate to your range of useable power (wider is better).
Be realistic in your estimates and plans - peak torque @ 7000 RPM sounds good, but is almost certainly beyond the breathing ability of even a professionally-built race motor, and if true will make the car impossible to launch. Note that 1-1/2" pipe is large enough for a 273" motor with max torque @ 4000 RPM. A 360" only needs 1-3/4"
for 4200 RPM. A 440" is fine @ 4500 RPM with 2" primaries."
What size do I need at peak torque @ 5000RPM ? Don't really matter cause I know they don't make 'em


He has a few things I don't agree with however, according to him, my useable power is only 1500RPM but I run all day with a power range anywhere from 1700RPM to 7500RPM

"Remember that your peak torque RPM will always be lower than your peak HP RPM. The separation between peak torque and peak power is roughly proportionate to your range of useable power (wider is better).
Be realistic in your estimates and plans - peak torque @ 7000 RPM sounds good, but is almost certainly beyond the breathing ability of even a professionally-built race motor, and if true will make the car impossible to launch. Note that 1-1/2" pipe is large enough for a 273" motor with max torque @ 4000 RPM. A 360" only needs 1-3/4"
for 4200 RPM. A 440" is fine @ 4500 RPM with 2" primaries."
What size do I need at peak torque @ 5000RPM ? Don't really matter cause I know they don't make 'em


Last edited by MotorHead; 11-12-2010 at 12:36 PM.
#73
Team Owner


#74
Le Mans Master



Its quiet at idle and cruise but it has a little sound to it at WOT......Listen for yourself....
http://www.youtube.com/watch?v=1MgUjxyaQog

#75
Safety Car


Member Since: Nov 2005
Location: Lompoc, CA. Santa Barbara County
Posts: 3,932
Received 543 Likes
on
198 Posts


Its quiet at idle and cruise but it has a little sound to it at WOT......Listen for yourself....
http://www.youtube.com/watch?v=1MgUjxyaQog

http://www.youtube.com/watch?v=1MgUjxyaQog


Bee Jay
#76
Melting Slicks


Member Since: May 2005
Location: Montgomery Alabama
Posts: 2,209
Likes: 0
Received 12 Likes
on
3 Posts
Cruise-In VII Veteran
St. Jude Donor '06


Bigger is not always better for TQ or HP. Bigger is not always better for 1.4 mile times. Bigger is not always better for sound.
Bigger is ALWAYS better for visual effect. that is why I have 4" pipes on the side of my car! If I was serious about my 1/4 mile times, I would put a built TH400 behind my big block, put some taller gears in the differential, put smaller primary sized headers on the engine, and run a smaller pipe out the back of the car. But where is the fun in that?
For the msot part, a 2.5" exhasut is better for the street. It also fits under the rear suspension easier.
Most custom exhaust shops can build a system for the same cost as any kit you would buy, have shipped to the house, carry to the exhaust shop, and have welded together.
I paid $400 to have a polished stainless steel 2.25" dual exhaust system with dual cats, dual resonators, an x-pipe, a dual-in dual-out x-muffler, and two polished tips installed. I carried all the Magnaflow parts to them to be installed and he even swapped out my original O2 sensors for that. I paid $400for the Magnaflow pieces that I carried to him. This was for my Infiniti Q45, which has the same set-up as the C3 with exhaust pipes running under the independent rear differential.
Bigger is ALWAYS better for visual effect. that is why I have 4" pipes on the side of my car! If I was serious about my 1/4 mile times, I would put a built TH400 behind my big block, put some taller gears in the differential, put smaller primary sized headers on the engine, and run a smaller pipe out the back of the car. But where is the fun in that?
For the msot part, a 2.5" exhasut is better for the street. It also fits under the rear suspension easier.
Most custom exhaust shops can build a system for the same cost as any kit you would buy, have shipped to the house, carry to the exhaust shop, and have welded together.
I paid $400 to have a polished stainless steel 2.25" dual exhaust system with dual cats, dual resonators, an x-pipe, a dual-in dual-out x-muffler, and two polished tips installed. I carried all the Magnaflow parts to them to be installed and he even swapped out my original O2 sensors for that. I paid $400for the Magnaflow pieces that I carried to him. This was for my Infiniti Q45, which has the same set-up as the C3 with exhaust pipes running under the independent rear differential.
#77
#78

Thanks for posting this Paul, but this discusses *primary* pipe length. We are debating post secondary pipe length. Every exhaust header for a sbc I have seen has a collector of 3" or 3.5". THe debate here is whether a 2.5" system post collector is better than a 3" system post collector.
FWIW my Ford GT with 550hp came with 3" from the factory
FWIW my Ford GT with 550hp came with 3" from the factory
As i was reading and trying to do some research myself, I cam accross this on another form... this is a cut and past...
http://www.hotrodders.com/forum/exha...ula-49188.html
interesting, ......

1bad80 sent me this in a PM... I thought it'd be helpful for other sheeple here.
exhaust
Exhaust Design Comments:
The concept that maximum power is obtained by zero pressure in the exhaust is only partially true. There should be absolutely
no back-pressure from the collector rearward, but the diameter of the system beginning with the exhaust valve is a compromise. The highest efficiency for the system requires a minimum speed for good exhaust gas velocity to insure that
gas does not "back up" into the chamber during overlap at low engine speeds, and that the "suction" (negative pressure pulse) effect of a resonant (tuned length) and/or collector (overlapping exhaust pulses) system is optimized.
To predict what primary size will be best for a specific motor, you must know where you want the engine to develop peak torque. If the existing torque peak is at bit lower RPM than you prefer (typical in under-cammed or stock motors), it can be "bumped" a bit by increasing the primary diameter. If the torque peak is too high (motor is "peaky", with no range and poor recovery from
gear changes), the peak can be adjusted down by using a smaller pipe. A change of 1/8" in the primary diameter will raise or lower the peak torque RPM by 500 or so.
This factor slightly overlaps the effect of primary pipe length, but the pipe length generally will not change the peak torque or the RPM at which it occurs. A length change has the effect of improving the torque on only 1 side of the peak by "borrowing" it from the other side. A shorter pipe improves the torque after the peak (reduces it at lower RPM), preventing the curve from
flattening out so quickly as speed increases.
A longer pipe extends the torque curve backwards to improve the engine's flexibility, at the expense of after-peak torque. Less stall speed is required, and the motor will pull taller gears; this re-tunes a 4-speed motor for better operation with Torqueflite, etc.
For best effect, the gas speed in the primary tube at the peak torque RPM should be about 240 feet per second. The formula to calculate pipe size is:
Area of Primary Pipe = RPM × Cylinder Size ÷ 88,200
This determines the pipe's cross-sectional area, from which we can calculate the ID. Typical exhaust pipes are 18ga. (wall thickness of .049"), so the OD will be .098" larger. From this we can construct a formula for an 8 cylinder motor, and factor in the 18ga. wall thickness:
Area of Primary Pipe = RPM × Motor Size ÷ 705,600
Pipe ID2 = RPM × Motor Size ÷ 705,600 ÷ .7854
Pipe ID2 = RPM × Motor Size ÷ 554,177
ID = (RPM × Motor Size ÷ 554,177).5
OD = (RPM × Motor Size ÷ 554,177).5 + .098"
The following Chart shows exhaust pipe outside diameter, based on this formula, for various motor sizes and speeds. To determine if your pipe size is large enough, search across the top row for your motor size (interpolate if in between 2 sizes), and then down that column for your current pipe OD. If the peak torque RPM in the left column is high enough, your pipe is not a
restriction. If the peak torque RPM is lower than where you feel your torque peak is, look for the pipe OD on the line with your torque RPM.
If your primary pipe's wall thickness is 16ga. (.059"), add .020" to the OD figure to compensate.
LA Motors: Pipe Size @ Peak Torque RPM vs. Motor Size
Motor Size273"318"340"360"392"410"
RPMPrimary Pipe Outside Diameter, Inches
30001.311.411.451.491.551.59
32501.361.461.511.551.611.65
35001.411.521.561.611.671.71
37501.461.561.611.661.731.76
40001.501.611.661.711.781.82
42501.541.661.711.761.831.87
45001.591.701.761.811.881.92
47501.631.751.811.851.931.97
50001.671.791.851.901.982.02
52501.711.831.891.942.032.07
55001.741.871.931.992.072.12
57501.781.911.982.032.112.16
60001.821.952.022.072.162.20
Note: 392" is 340/360 block stroked with 3.79" crank; 410" is 340/360 block
stroked with 4.00" crank
B/RB Motors: Pipe Size @ Peak Torque RPM vs. Motor Size
Motor Size383"400"426"440"451"494"
RPMPrimary Pipe Outside Diameter, Inches
30001.541.571.621.641.661.73
32501.601.631.681.701.721.80
35001.651.691.741.771.791.86
37501.711.741.801.821.841.93
40001.761.801.851.881.901.99
42501.811.851.911.931.962.04
45001.861.901.961.992.012.10
47501.911.952.012.042.062.16
50001.962.002.062.092.122.21
52502.002.042.112.142.172.26
55002.052.092.152.192.212.31
57502.092.142.202.232.262.36
60002.132.182.252.282.312.41
Note: 451" is 400 block stroked with 440 crank; 494" is 400/440 block stroker
with 4.15" crank
Remember that your peak torque RPM will always be lower than your peak HP
RPM. The separation between peak torque and peak power is roughly
proportionate to your range of useable power (wider is better). Be realistic in your
estimates and plans - peak torque @ 7000 RPM sounds good, but is almost certainly
beyond the breathing ability of even a professionally-built race motor, and if
true will make the car impossible to launch. Note that 1-1/2" pipe is large
enough for a 273" motor with max torque @ 4000 RPM. A 360" only needs 1-3/4"
for 4200 RPM. A 440" is fine @ 4500 RPM with 2" primaries.
If choosing pipes for a 4WD, van, towing, etc. keep the size small to
improve torque where you need it most - the lower RPM ranges, typically 2500-3500.
One exception where use of a larger pipe (than indicated by the above
formula) will help power is, of course, motors using nitrous oxide, supercharger
or turbocharger. In these cases, size the pipe for the expected peak torque,
not the motor size.
Another instance where a slightly larger pipe may help is where the
departure angle of the pipe from the flange is very sharp (typically downward). The
added cross-sectional area immediately after the flange apparently helps
reduce the restrictive effect of a small radius after the port. This partially
explains why some header models or brands work better than others with similar
dimensions.
Minor Improvements
If possible, slightly enlarge the inside of the flange opening in the
header itself to produce a sharp step (be careful of grinding off the tube weld).
Do not radius the edge. A 1/16" bevel is generally possible and will help. If
there is not much room, don't grind all the way into the flange - a 45° angle
is fine. This has a minor anti-reversion effect, helping to prevent back-flow
at low engine speeds; helps clean up idle quality, etc.
If the primary pipe inside diameter is more than 1/8" larger than the
actual port opening in the head, the header flange bolt pattern can be slotted
slightly to raise the centerline of the primary pipe above the center of the
port, until the bottom of the pipe just matches. This puts the pipe's effective
center closer to the most active area of gas flow, and the mis-alignment at the
roof allows the highest-pressure gas an easier path away from the port; also
adds some degree of anti-reversion.
If controlling reversion is more important than maximum port flow (e.g.
primary diameter is very large), Vizard suggests the mis-match should be at the
bottom of the port where gas flow is slowest, and therefore most likely to
reverse-flow at low engine speed.
An easy way to effect a small increase in exhaust efficiency, if space
permits, is to move the header out away from the port by 1/2" or more (using an
extra gasket and longer studs or bolts). This moves the restrictive angle
farther away from the port - every little bit helps here. It also reduces local
exhaust port temperature in the head slightly. An easy spacer is an extra header
flange or 2, but be sure that the transition from the extra flange to the
header is not restricted. The extra flange may be slightly larger than the port
opening in the head, but must not step down entering the header. Do not taper,
blend, or bevel the extra flange to act as a transition between the port and
the header.
Anti-Reversion Plate
If the header in use is substantially larger than other available choices
for the same motor (i.e., you're using 2" OD, but headers are also available
in 1-5/8", etc.), an inexpensive anti-reversion plate can be made from a bare
flange with the smaller size (1-5/8"). Do these steps in order:
» Match the extra flange openings to the exhaust ports.
» Lay it over your actual 2" header flange.
» Spray paint, mark etc. the 2" openings around the 1-5/8" openings (they
will
be concentric circles).
» Remove the marked area as shown, using ball end carbide, etc.
I would suggest the following rules for best effect:
» The extra, smaller flange be no smaller than your motor's exhaust port.
» The extra flange be at least 1/4" smaller than the header in use (if
using a
header with 2" primaries, the extra flange should be 1-3/4" maximum).
» Make sure there's enough room to move both sides of the header away
from the motor by 3/8" or so (the header flange thickness).
» You may need an extra gasket between the flanges, or sealer may do
(Vizard uses silicone here)
» Longer bolts or studs will probably be needed; remember to use sealant on
B/RB motors due to water in holes.
and more:
http://victorylibrary.com/mopar/header-tech-c.htm
http://www.bgsoflex.com/bestheader.html
http://www.hotrodders.com/forum/exha...ula-49188.html
interesting, ......


1bad80 sent me this in a PM... I thought it'd be helpful for other sheeple here.
exhaust
Exhaust Design Comments:
The concept that maximum power is obtained by zero pressure in the exhaust is only partially true. There should be absolutely
no back-pressure from the collector rearward, but the diameter of the system beginning with the exhaust valve is a compromise. The highest efficiency for the system requires a minimum speed for good exhaust gas velocity to insure that
gas does not "back up" into the chamber during overlap at low engine speeds, and that the "suction" (negative pressure pulse) effect of a resonant (tuned length) and/or collector (overlapping exhaust pulses) system is optimized.
To predict what primary size will be best for a specific motor, you must know where you want the engine to develop peak torque. If the existing torque peak is at bit lower RPM than you prefer (typical in under-cammed or stock motors), it can be "bumped" a bit by increasing the primary diameter. If the torque peak is too high (motor is "peaky", with no range and poor recovery from
gear changes), the peak can be adjusted down by using a smaller pipe. A change of 1/8" in the primary diameter will raise or lower the peak torque RPM by 500 or so.
This factor slightly overlaps the effect of primary pipe length, but the pipe length generally will not change the peak torque or the RPM at which it occurs. A length change has the effect of improving the torque on only 1 side of the peak by "borrowing" it from the other side. A shorter pipe improves the torque after the peak (reduces it at lower RPM), preventing the curve from
flattening out so quickly as speed increases.
A longer pipe extends the torque curve backwards to improve the engine's flexibility, at the expense of after-peak torque. Less stall speed is required, and the motor will pull taller gears; this re-tunes a 4-speed motor for better operation with Torqueflite, etc.
For best effect, the gas speed in the primary tube at the peak torque RPM should be about 240 feet per second. The formula to calculate pipe size is:
Area of Primary Pipe = RPM × Cylinder Size ÷ 88,200
This determines the pipe's cross-sectional area, from which we can calculate the ID. Typical exhaust pipes are 18ga. (wall thickness of .049"), so the OD will be .098" larger. From this we can construct a formula for an 8 cylinder motor, and factor in the 18ga. wall thickness:
Area of Primary Pipe = RPM × Motor Size ÷ 705,600
Pipe ID2 = RPM × Motor Size ÷ 705,600 ÷ .7854
Pipe ID2 = RPM × Motor Size ÷ 554,177
ID = (RPM × Motor Size ÷ 554,177).5
OD = (RPM × Motor Size ÷ 554,177).5 + .098"
The following Chart shows exhaust pipe outside diameter, based on this formula, for various motor sizes and speeds. To determine if your pipe size is large enough, search across the top row for your motor size (interpolate if in between 2 sizes), and then down that column for your current pipe OD. If the peak torque RPM in the left column is high enough, your pipe is not a
restriction. If the peak torque RPM is lower than where you feel your torque peak is, look for the pipe OD on the line with your torque RPM.
If your primary pipe's wall thickness is 16ga. (.059"), add .020" to the OD figure to compensate.
LA Motors: Pipe Size @ Peak Torque RPM vs. Motor Size
Motor Size273"318"340"360"392"410"
RPMPrimary Pipe Outside Diameter, Inches
30001.311.411.451.491.551.59
32501.361.461.511.551.611.65
35001.411.521.561.611.671.71
37501.461.561.611.661.731.76
40001.501.611.661.711.781.82
42501.541.661.711.761.831.87
45001.591.701.761.811.881.92
47501.631.751.811.851.931.97
50001.671.791.851.901.982.02
52501.711.831.891.942.032.07
55001.741.871.931.992.072.12
57501.781.911.982.032.112.16
60001.821.952.022.072.162.20
Note: 392" is 340/360 block stroked with 3.79" crank; 410" is 340/360 block
stroked with 4.00" crank
B/RB Motors: Pipe Size @ Peak Torque RPM vs. Motor Size
Motor Size383"400"426"440"451"494"
RPMPrimary Pipe Outside Diameter, Inches
30001.541.571.621.641.661.73
32501.601.631.681.701.721.80
35001.651.691.741.771.791.86
37501.711.741.801.821.841.93
40001.761.801.851.881.901.99
42501.811.851.911.931.962.04
45001.861.901.961.992.012.10
47501.911.952.012.042.062.16
50001.962.002.062.092.122.21
52502.002.042.112.142.172.26
55002.052.092.152.192.212.31
57502.092.142.202.232.262.36
60002.132.182.252.282.312.41
Note: 451" is 400 block stroked with 440 crank; 494" is 400/440 block stroker
with 4.15" crank
Remember that your peak torque RPM will always be lower than your peak HP
RPM. The separation between peak torque and peak power is roughly
proportionate to your range of useable power (wider is better). Be realistic in your
estimates and plans - peak torque @ 7000 RPM sounds good, but is almost certainly
beyond the breathing ability of even a professionally-built race motor, and if
true will make the car impossible to launch. Note that 1-1/2" pipe is large
enough for a 273" motor with max torque @ 4000 RPM. A 360" only needs 1-3/4"
for 4200 RPM. A 440" is fine @ 4500 RPM with 2" primaries.
If choosing pipes for a 4WD, van, towing, etc. keep the size small to
improve torque where you need it most - the lower RPM ranges, typically 2500-3500.
One exception where use of a larger pipe (than indicated by the above
formula) will help power is, of course, motors using nitrous oxide, supercharger
or turbocharger. In these cases, size the pipe for the expected peak torque,
not the motor size.
Another instance where a slightly larger pipe may help is where the
departure angle of the pipe from the flange is very sharp (typically downward). The
added cross-sectional area immediately after the flange apparently helps
reduce the restrictive effect of a small radius after the port. This partially
explains why some header models or brands work better than others with similar
dimensions.
Minor Improvements
If possible, slightly enlarge the inside of the flange opening in the
header itself to produce a sharp step (be careful of grinding off the tube weld).
Do not radius the edge. A 1/16" bevel is generally possible and will help. If
there is not much room, don't grind all the way into the flange - a 45° angle
is fine. This has a minor anti-reversion effect, helping to prevent back-flow
at low engine speeds; helps clean up idle quality, etc.
If the primary pipe inside diameter is more than 1/8" larger than the
actual port opening in the head, the header flange bolt pattern can be slotted
slightly to raise the centerline of the primary pipe above the center of the
port, until the bottom of the pipe just matches. This puts the pipe's effective
center closer to the most active area of gas flow, and the mis-alignment at the
roof allows the highest-pressure gas an easier path away from the port; also
adds some degree of anti-reversion.
If controlling reversion is more important than maximum port flow (e.g.
primary diameter is very large), Vizard suggests the mis-match should be at the
bottom of the port where gas flow is slowest, and therefore most likely to
reverse-flow at low engine speed.
An easy way to effect a small increase in exhaust efficiency, if space
permits, is to move the header out away from the port by 1/2" or more (using an
extra gasket and longer studs or bolts). This moves the restrictive angle
farther away from the port - every little bit helps here. It also reduces local
exhaust port temperature in the head slightly. An easy spacer is an extra header
flange or 2, but be sure that the transition from the extra flange to the
header is not restricted. The extra flange may be slightly larger than the port
opening in the head, but must not step down entering the header. Do not taper,
blend, or bevel the extra flange to act as a transition between the port and
the header.
Anti-Reversion Plate
If the header in use is substantially larger than other available choices
for the same motor (i.e., you're using 2" OD, but headers are also available
in 1-5/8", etc.), an inexpensive anti-reversion plate can be made from a bare
flange with the smaller size (1-5/8"). Do these steps in order:
» Match the extra flange openings to the exhaust ports.
» Lay it over your actual 2" header flange.
» Spray paint, mark etc. the 2" openings around the 1-5/8" openings (they
will
be concentric circles).
» Remove the marked area as shown, using ball end carbide, etc.
I would suggest the following rules for best effect:
» The extra, smaller flange be no smaller than your motor's exhaust port.
» The extra flange be at least 1/4" smaller than the header in use (if
using a
header with 2" primaries, the extra flange should be 1-3/4" maximum).
» Make sure there's enough room to move both sides of the header away
from the motor by 3/8" or so (the header flange thickness).
» You may need an extra gasket between the flanges, or sealer may do
(Vizard uses silicone here)
» Longer bolts or studs will probably be needed; remember to use sealant on
B/RB motors due to water in holes.
and more:
http://victorylibrary.com/mopar/header-tech-c.htm
http://www.bgsoflex.com/bestheader.html
#79

This sounds like a smokin deal if the your Infinity has as much fabrication required as a Corvette.
It is important to keep in mind that we are not debating whether "bigger is better" but rather whether 3" is better than 2.5" for a covette that produces 440hp at the rear wheels. This is very close to the C6 Z06 which, I think, uses a 3" system.
I currently have side pipes on my 65 Fuelie and plan to convert to a 2.5 undercar system (mandrel bends and X pipe) next winter. This winter is booked with projects already.
Mike
It is important to keep in mind that we are not debating whether "bigger is better" but rather whether 3" is better than 2.5" for a covette that produces 440hp at the rear wheels. This is very close to the C6 Z06 which, I think, uses a 3" system.
I currently have side pipes on my 65 Fuelie and plan to convert to a 2.5 undercar system (mandrel bends and X pipe) next winter. This winter is booked with projects already.
Mike
Bigger is not always better for TQ or HP. Bigger is not always better for 1.4 mile times. Bigger is not always better for sound.
Bigger is ALWAYS better for visual effect. that is why I have 4" pipes on the side of my car! If I was serious about my 1/4 mile times, I would put a built TH400 behind my big block, put some taller gears in the differential, put smaller primary sized headers on the engine, and run a smaller pipe out the back of the car. But where is the fun in that?
For the msot part, a 2.5" exhasut is better for the street. It also fits under the rear suspension easier.
Most custom exhaust shops can build a system for the same cost as any kit you would buy, have shipped to the house, carry to the exhaust shop, and have welded together.
I paid $400 to have a polished stainless steel 2.25" dual exhaust system with dual cats, dual resonators, an x-pipe, a dual-in dual-out x-muffler, and two polished tips installed. I carried all the Magnaflow parts to them to be installed and he even swapped out my original O2 sensors for that. I paid $400for the Magnaflow pieces that I carried to him. This was for my Infiniti Q45, which has the same set-up as the C3 with exhaust pipes running under the independent rear differential.
Bigger is ALWAYS better for visual effect. that is why I have 4" pipes on the side of my car! If I was serious about my 1/4 mile times, I would put a built TH400 behind my big block, put some taller gears in the differential, put smaller primary sized headers on the engine, and run a smaller pipe out the back of the car. But where is the fun in that?
For the msot part, a 2.5" exhasut is better for the street. It also fits under the rear suspension easier.
Most custom exhaust shops can build a system for the same cost as any kit you would buy, have shipped to the house, carry to the exhaust shop, and have welded together.
I paid $400 to have a polished stainless steel 2.25" dual exhaust system with dual cats, dual resonators, an x-pipe, a dual-in dual-out x-muffler, and two polished tips installed. I carried all the Magnaflow parts to them to be installed and he even swapped out my original O2 sensors for that. I paid $400for the Magnaflow pieces that I carried to him. This was for my Infiniti Q45, which has the same set-up as the C3 with exhaust pipes running under the independent rear differential.